In modern factories, manufacturing plants, and industrial zones, overhead cranes play a pivotal role in the safe and efficient handling of heavy materials. This article provides an in-depth look at the types of industrial cranes offered by PREBECC, our streamlined fabrication process, and why our solutions are consistently chosen for major industrial projects.
1. Industrial cranes and their applications
How do you safely, precisely, and cost-effectively lift and transport heavy loads in today’s industrial environments? That’s the core challenge industrial crane systems are designed to solve.
Industrial cranes are mechanical systems engineered for lifting, lowering, and moving heavy objects within a defined workspace. Through a combination of girders, hoists, and specialized drive mechanisms, cranes reduce reliance on manual labor while improving operational efficiency.
Their role in factories, warehouses, and production lines is indispensable. Cranes help:
- Boost productivity and shorten handling time
- Reduce labor costs and improve overall operational efficiency
- Enhance workplace safety and minimize lifting-related injuries
- Optimize floor space and support flexible automation workflows
Today, industrial cranes are utilized across a wide range of sectors including steel manufacturing, heavy machinery, shipbuilding, energy, cement, food processing, and logistics – each requiring different crane configurations such as single girder, double girder, suspension, jib, gantry, and semi-gantry types.
2. Types of tndustrial cranes supplied by PREBECC
Single Girder Overhead Crane
- Compact and cost-effective design, ideal for facilities with height constraints
- Common lifting capacities range from 1 to 20 tons
- Easy to install and maintain, offering excellent ROI
Double Girder Overhead Crane
- Features two main girders for enhanced load-bearing capacity (10 to 100 tons or more)
- Suitable for heavy-duty applications and lifting oversized components
- Can be equipped with maintenance walkways and rail tracks for auxiliary systems
Suspension Crane
- Mounted directly to the roof structure of the building
- Ideal for limited-space environments or where supporting columns for runway beams are not feasible
Gantry Crane
Operates on rails mounted on the ground, independent of building structure
Options include:
Single Girder Gantry Crane: Lightweight, budget-friendly, for moderate loads
Double Girder Gantry Crane: High load capacity, stable performance for large-scale operations
Jib Crane
Compact and versatile, often used at standalone workstations
Offers a wide slewing range, enabling localized and precise load handling
Customized Specialty Cranes
PREBECC also designs and manufactures purpose-built crane systems, including: Cleanroom cranes; Explosion-proof cranes; Mobile cranes
These systems are tailored to meet stringent technical standards and specialized operational requirements across various industries.
At PREBECC, we are committed to providing highly customizable crane solutions tailored to your space constraints, load requirements, and operational needs. Every crane system we deliver is engineered for safety, reliability, and maximum performance – built to comply with TCVN standards and beyond.
3. Industrial crane fabrication process at PREBECC
The quality and reliability of a crane system stem not only from its design but also significantly from the fabrication process and rigorous quality control at every production stage. With years of experience in the design, manufacturing, and installation of cranes, PREBECC has established a systematic, science-based fabrication process that strictly adheres to technical standards such as ISO, TCVN, FEM, etc. This ensures that every delivered product achieves optimal performance and absolute operational safety.
3.1. Request tntake – Site survey – Preliminary design consultation
Upon receiving a customer request, PREBECC’s engineering team proceeds to:
- Conduct on-site surveys or analyze the structural drawings of the facility.
- Assess operational conditions, load requirements, and duty cycles.
- Recommend the most suitable crane type (single girder, double girder, gantry, jib crane, etc.) based on usage needs and investment budget.
The consultation goes beyond equipment selection—it aims to offer an optimized overall solution, including layout design, installation space, power supply, control systems, and future maintenance plans.
3.2. Technical design – Detailed drawings
Once the preliminary plan is approved, PREBECC proceeds with technical design:
- Utilize specialized software like AutoCAD Mechanical and SolidWorks to create 2D/3D drawings and operational simulations.
- Precisely calculate load capacities, moments, lifting forces, inertial forces, lifting height, span dimensions, etc.
- Select appropriate hoists, drive mechanisms, and control systems.
- All drawings undergo strict review and approval before moving to the fabrication stage.
3.3. Material selection – Synchronized equipment
Materials and components are critical to the crane system’s durability and safety:
- Use high-quality structural steel such as SS400, Q345B (or equivalents like JIS, ASTM) to ensure mechanical strength and load-bearing capacity.
- Verify all materials with Certificates of Origin and Quality (CO-CQ).
- Select motors, hoists, gearboxes, inverters, and PLCs from reputable brands such as Hitachi, Schneider, Siemens, Sungdo, etc.
3.4. Precision machining – Structural welding
Fabrication is carried out at PREBECC’s facility using advanced machinery:
- CNC plasma/laser cutting, turning, milling, and drilling for high-precision components.
- MIG/MAG and SAW semi-automatic welding, following approved WPS procedures.
- Weld quality is inspected using non-destructive testing (NDT) methods: ultrasonic testing (UT), radiographic testing (RT), when required.
3.5. Quality inspection – Mechanical test assembly
Before full assembly:
- Structural components are checked for dimensions, tolerances, flatness, and parallelism using specialized equipment.
- Pre-assembly of subcomponents ensures compatibility and ease of on-site installation.
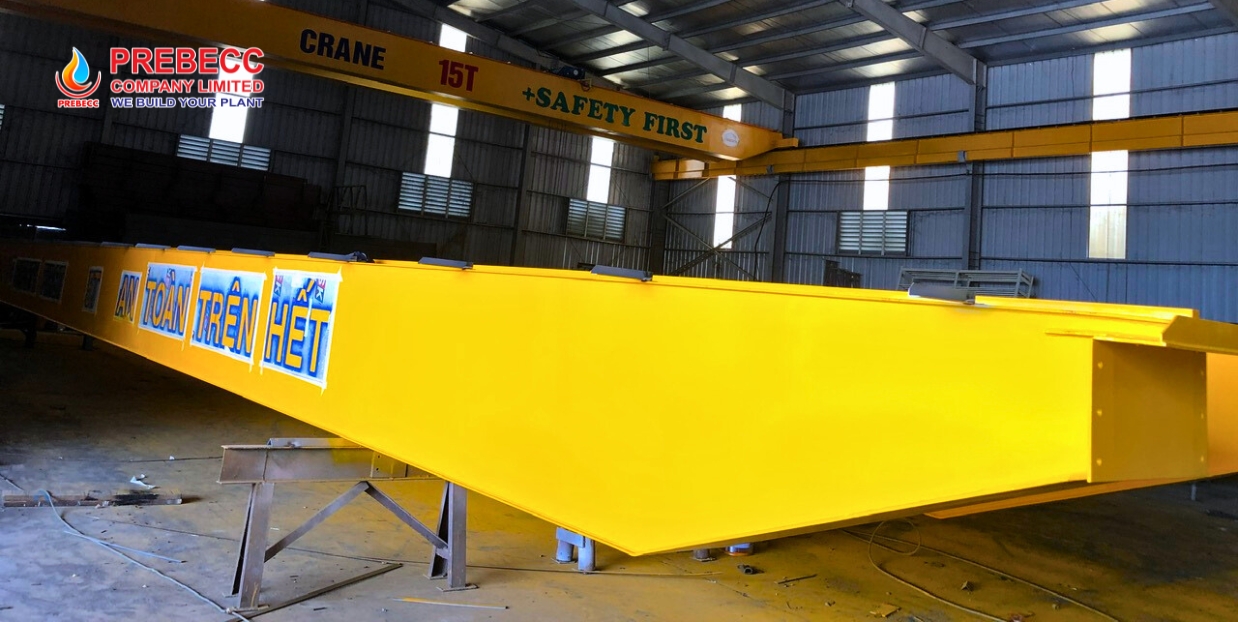
3.6. Protective coating – Corrosion resistance
All steel surfaces are treated for rust prevention and final coating as per ISO 12944 standards:
- Use of 2-component epoxy or polyurethane paints to protect against corrosion in heavy industrial and coastal environments.
- Color schemes can follow customer branding or specific requests.
3.7. Final assembly – Comprehensive testing
The crane system is fully assembled and tested at the factory before delivery:
- Electrical systems, drives, hoists, rails, and safety devices are all thoroughly checked.
- Load testing (both static and dynamic) is performed to meet technical safety standards.
If required, PREBECC coordinates with certified inspection bodies appointed by the Ministry of Labor, Invalids and Social Affairs.
3.8. Transport – On-Site installation – Handover
Equipment is transported to the site using specialized vehicles.
PREBECC’s experienced technicians handle installation, alignment, and test runs on-site.
Timely handover includes operational training and transfer of technical documentation to the customer.
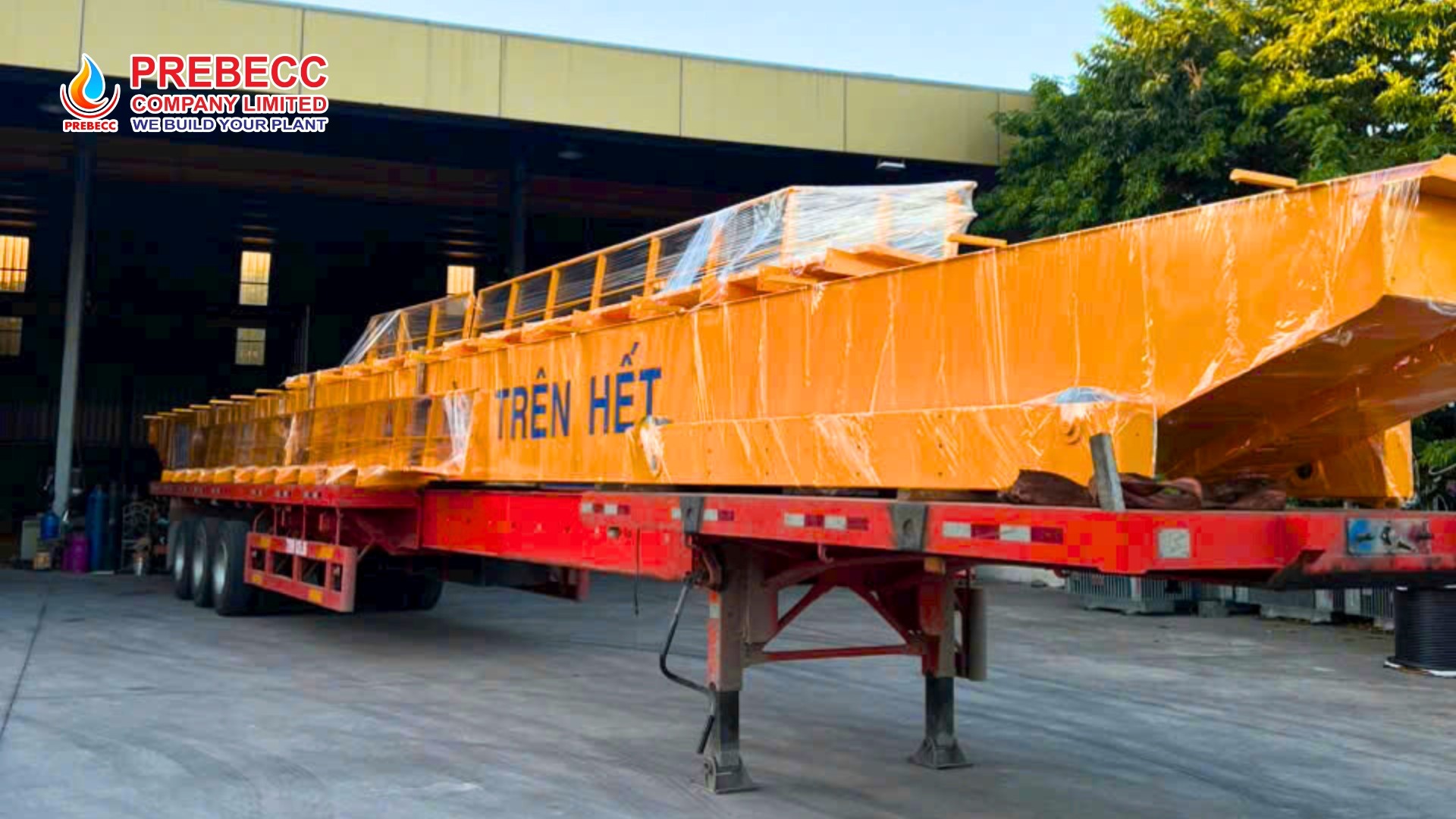
4. Quotation & Service consultation
Are you looking for a trusted, professional partner to fabricate industrial cranes—one who will accompany you through every stage, from design to installation? Let PREBECC help you optimize the most suitable lifting solution for your needs.
📞 Call our hotline: (+84) 708091033
📧 Email us at: info@prebecc.com
Our technical team is ready to provide detailed consultation and a prompt quotation.