As climate change becomes an ever-growing global concern, carbon reduction is no longer optional — it’s a survival imperative for every industry. From Europe to Asia, governments are tightening environmental regulations, requiring businesses to reduce greenhouse gas emissions during production. Meanwhile, consumers increasingly prefer eco-friendly products with transparent environmental impacts and social responsibility.
This raises a critical question:
How can businesses stay compliant, cut operational costs, and demonstrate environmental responsibility — all at once?
The answer lies not in paperwork, but in choosing the right production technology. Among these, the energy efficient boiler is emerging as a key solution. More than just reducing fuel consumption and running costs, these systems directly cut CO₂ emissions, helping companies move closer to their carbon neutrality goals.
More than a technical upgrade, energy efficient boilers are a strategic investment — a gateway to global markets where environmental and ESG standards are increasingly stringent. Adopting this technology not only boosts competitiveness, but also builds a sustainable brand image in the eyes of partners and consumers alike.
1. The challenge of traditional boilers in a changing world
In today’s industrial systems, boilers are essential for steam generation – powering heating, drying, sterilization, or mechanical operations. However, in Vietnam and many developing countries, most businesses still rely on traditional fossil-fueled boilers, using coal, heavy oil (FO), or liquefied gas.
This results in serious environmental and economic consequences – including legal non-compliance and reduced competitiveness in export markets.
1.1 When steam becomes an invisible pollutant
Traditional boilers – especially coal or oil-fired are notoriously inefficient, converting only 60-75% of input energy into usable steam. That means 25-40% is wasted as exhaust, radiation, or losses due to poor heat exchange (Source: Energy Efficiency Guide for Industry in Asia, UNIDO).
Each ton of fossil fuel burned releases massive amounts of harmful emissions, with CO₂ (Carbon Dioxide) being the chief culprit in global warming. For example, burning one ton of coal emits approximately 2.86 tons of CO₂ (IPCC Guidelines, 2006).
Additionally, NOₓ (Nitrogen Oxides) and SOₓ (Sulfur Oxides) contribute to acid rain, damaging ecosystems, water sources, and infrastructure. In coal-fired plants without flue gas treatment, SO₂ levels can reach 1,500–2,500 mg/Nm³, far above Vietnam’s current environmental standards.
PM2.5 fine dust, a byproduct of incomplete combustion, poses severe long-term health risks to workers and nearby communities if not properly controlled.
1.2. Draining resources: The hidden cost of fossil-fueled boilers
Traditional boilers depend on fossil fuels, a non-renewable energy source with highly unstable pricing. Reports from the International Energy Agency (IEA) and national energy authorities like Vietnam’s Ministry of Industry and Trade continue to show rising coal and fuel oil prices. For example, between 2020 and 2023, global FO (fuel oil) prices increased by more than 40 percent during certain periods due to geopolitical tension and market fluctuations.
A typical 3 TPH (tons per hour) boiler operating 20 hours per day can consume around 500 to 600 liters of fuel oil daily. At an average market price of 17,000 to 20,000 VND per liter (as of June 2025), the annual fuel cost can reach 8 to 10 billion VND. Even more concerning, poor boiler efficiency may cause an additional 2 to 3 billion VND in energy losses each year. These losses, often overlooked, do not contribute to useful steam generation and instead become a major hidden cost.
1.3. Legal pressure: Compliance is no longer optional
In Vietnam, environmental regulations are becoming stricter and more aligned with global standards. The National Technical Regulation on Industrial Emissions (QCVN 22:2022/BTNMT), effective from January 15, 2023, sets clear limits based on boiler type, fuel, and capacity. For coal-fired boilers, carbon monoxide must be kept under 500 mg/Nm³, and sulfur dioxide between 500 to 1,200 mg/Nm³, depending on capacity and location. Violations are subject to strict enforcement.
Vietnam’s Environmental Protection Law 2020, in effect since January 1, 2022, also strengthens corporate responsibility. Businesses that exceed emission limits may face fines of up to 2 billion VND for individuals and up to 4 billion VND for organizations. Continued violations may even result in forced suspension of operations.
Internationally, the pressure is increasing. The EU’s Carbon Border Adjustment Mechanism (CBAM), effective from 2026, will require importers of high-emission goods to declare embedded CO₂ emissions and purchase carbon certificates. This will raise export costs significantly for producers using energy-intensive technologies.
Likewise, the EU Ecodesign Directive and Energy Labelling Regulation establish minimum energy performance standards for a wide range of products. These standards are shaping the expectations of European buyers and partners.
All signs make one thing clear. Relying on outdated boiler systems is no longer a viable option for companies with global ambitions. Investing in an energy efficient boiler is not just about compliance. It is a forward-thinking decision to secure competitiveness and build long-term resilience.
2. Emission reduction mechanism of energy efficient boilers
Reducing greenhouse gas emissions from industrial boiler systems requires more than cautious operation or passive control. It involves a complete technological restructuring – with the energy efficient boiler at the core, thanks to its system-wide innovations in combustion, heat transfer, and fuel optimization.
Far from being just an upgraded version of legacy boilers, this is a high-performance ecosystem, built for maximum efficiency and environmental sustainability.
2.1. Clean combustion technology – Optimizing the burn process
At the heart of every boiler is the combustion chamber, where fuel is converted into thermal energy. In traditional boilers, combustion is often incomplete due to poor air-fuel control or outdated chamber design, leading to excess pollutants such as carbon monoxide (CO), fine particulate matter (PM2.5), nitrogen oxides (NOₓ), and sulfur oxides (SOₓ).
In contrast, energy efficient boilers are engineered with advanced combustion technologies to ensure cleaner and more complete fuel burn:
Forced Draft Combustion with inverter control
Equipped with variable-speed fans and intelligent control systems, the boiler precisely regulates airflow into the combustion chamber. This maintains an optimal air-fuel ratio, close to the stoichiometric ratio, allowing for complete combustion and minimal formation of CO or unburned hydrocarbons.
Fluidized Bed Combustion (FBC)
This technique burns fuel within a suspended bed of particles (typically sand) agitated by high-velocity air, delivering several key advantages:
- Even heat distribution ensures consistent combustion across the chamber.
- Reduced NOₓ emissions due to lower combustion temperatures compared to conventional burners.
- In-situ SOₓ removal using limestone or other sorbents added directly to the bed to absorb sulfur during combustion.
Oxygen trim control system
Real-time oxygen sensors in the flue gas continuously monitor excess O₂ levels. The data feeds back to the central controller to automatically adjust the airflow, ensuring optimal oxygen levels for complete combustion. This prevents both energy loss from too much air and pollutant formation from too little.
According to studies by the Asian Industrial Energy Efficiency Project (UNIDO), adopting these advanced combustion systems can reduce CO₂ and NOₓ emissions by 30-50% and cut fuel consumption by up to 20%, depending on operating conditions and fuel type.
Energy efficient boilers are not just cleaner – they are smarter, enabling manufacturers to achieve sustainability goals without sacrificing performance.
2.2. Waste heat recovery – Capturing unused energy
One of the primary reasons for low efficiency in traditional boilers is the loss of waste heat, particularly through flue gases and equipment surfaces. In boilers without a recovery system, flue gas temperatures can reach 200–300°C — translating to roughly 25–30% of input energy being lost.
An energy efficient boiler overcomes this challenge by integrating high-performance heat recovery components:
Flue gas economizer or Air preheater
These are heat exchangers installed along the exhaust line to reclaim residual heat from flue gases. An economizer uses this waste heat to preheat the boiler feedwater, while an air preheater warms up the combustion air. Both significantly reduce the energy demand from the primary fuel source and improve overall boiler efficiency.
Condensing boiler technology
This advanced solution captures latent heat from the water vapor in flue gases by lowering the exhaust temperature below the dew point. As the steam condenses, it releases significant thermal energy, which is reused within the system. Under optimal conditions, condensing boilers can achieve thermal efficiencies of 92–95%, especially when using natural gas.
Beyond fuel savings, heat recovery systems also lower flue gas temperatures to meet environmental standards like Vietnam’s QCVN 22:2022/BTNMT or the EU’s Ecodesign Directive, simplifying compliance for manufacturers.
2.3. Alternative fuels – A path to carbon neutral rteam production
In addition to combustion and heat recovery technology, the fuel source plays a critical role in reducing carbon emissions. Traditional boilers typically rely on fossil fuels like coal and heavy fuel oil (HFO), which have high CO₂ emission factors:
– Coal (anthracite or bituminous): Approximately 2.86 tons of CO₂ per ton burned
– Fuel oil (FO): Roughly 3.14 tons of CO₂ per ton burned
(Source: IPCC Emission Factors, 2006)
To align with carbon reduction goals, modern energy efficient boilers are designed to support or encourage cleaner fuel alternatives:
Biomass Combustion
Biomass fuels, such as rice husks, sawdust, coffee husks, and wood chips, are renewable by-products from agriculture and forestry. In a closed biological cycle, biomass is considered carbon neutral, since the CO₂ released during combustion is reabsorbed by plants through photosynthesis. This not only lowers net emissions but also adds value to agricultural waste.
Liquefied Natural Gas (LNG)
LNG is a cleaner-burning fossil fuel that produces 20–30% less CO₂ than fuel oil and emits fewer particulates and sulfur oxides. It’s especially well-suited for industries requiring a clean production environment, such as food and pharmaceuticals.
Hybrid Fuel Flexibility
Many advanced boilers support dual-fuel or multi-fuel systems – enabling operations to switch or blend fuels such as biomass with coal, or LNG with diesel. This flexibility allows businesses to optimize costs amid fluctuating fuel markets while taking advantage of each fuel’s environmental benefits.
According to the International Energy Agency (IEA), switching from fuel oil to biomass can reduce CO₂ emissions by up to 70–80%, making it a vital strategy in the global effort to reach net-zero emissions by 2050.
Selecting the right fuel mix is no longer just about energy cost – it’s a cornerstone of sustainable and responsible industrial manufacturing.
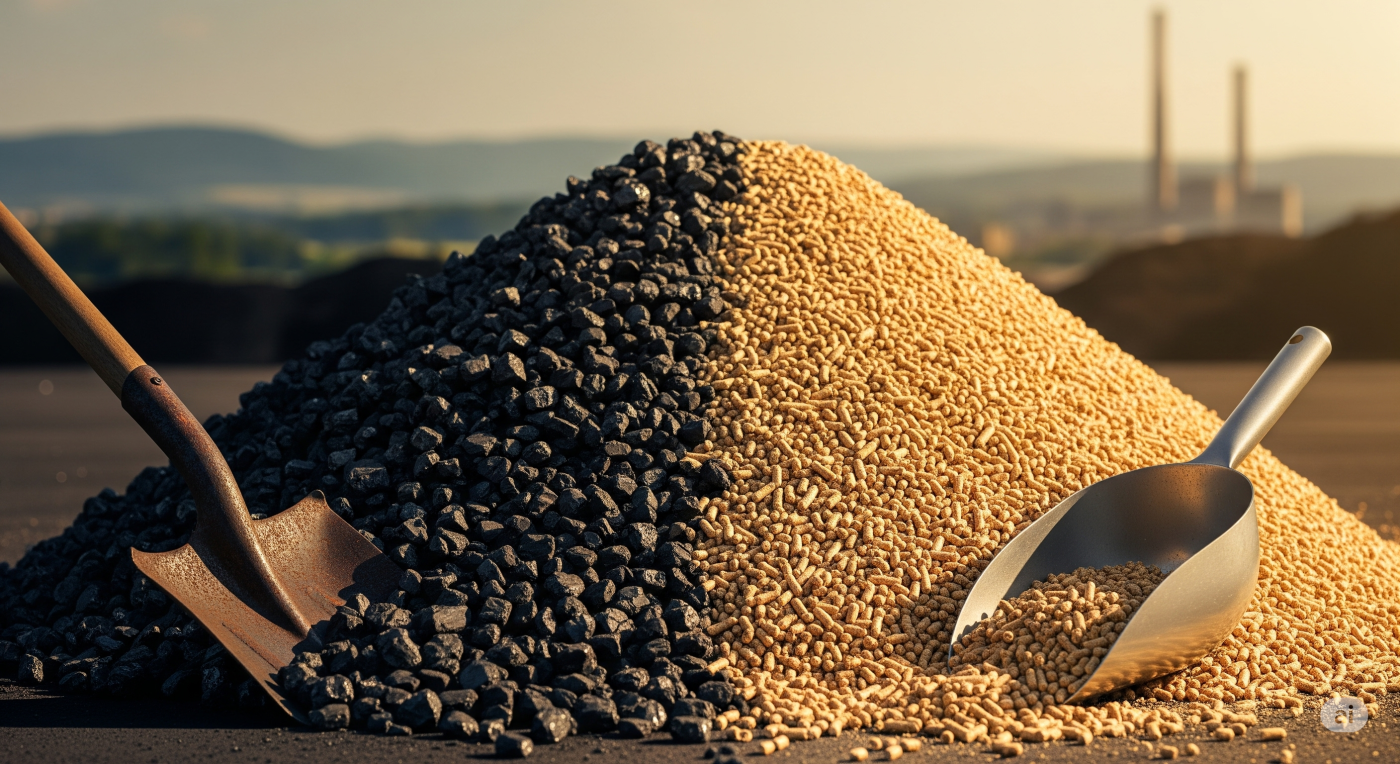
3. Implementation challenges and solutions
While an energy efficient boiler brings clear environmental and financial benefits, the transition process isn’t always smooth. From field experience across energy-intensive sectors—such as food processing, chemicals, textiles, and packaging—three main challenges frequently arise. Each requires a tailored solution and a well-defined roadmap.
3.1. High initial investment costs
Replacing depreciated, conventional boilers with high-efficiency models—such as those using fluidized bed combustion, advanced heat recovery systems, or smart energy management—requires significant upfront capital. Investment can range from tens of thousands to hundreds of thousands of USD, depending on boiler capacity and technology, posing a barrier for small and medium-sized enterprises (SMEs).
Practical solutions:
Green financing & bank partnerships: Many banks and international institutions (e.g., IFC) offer green loans with lower interest rates (2–3% below market average) or flexible repayment terms specifically for energy efficiency projects.
Government support schemes: Vietnam’s Ministry of Industry and Trade, via the National Energy Efficiency Program (VNEEP), provides subsidies covering up to 30–50% of energy audit costs and offers expert technical consultancy.
Equipment leasing / Energy-as-a-Service (EaaS): Some domestic and global boiler vendors now offer leasing models where companies pay per ton of steam used – eliminating the need for capital investment while gaining full access to modern technology.
3.2. Skills gap for operating modern systems
Another concern is that energy efficient boiler systems may be more complex to operate, requiring trained personnel familiar with clean combustion, heat optimization, and modern maintenance protocols. This raises concerns around training costs and technical readiness.
Solution: Reputable boiler suppliers in Vietnam and abroad often offer turnkey services, including hands-on training, remote technical support, and long-term warranties (2-5 years), allowing businesses to rapidly adopt and master new systems.
3.3. Roadmap to deployment – From audit to carbon savings
Transitioning to an energy efficient boiler should be planned, not rushed. A phased roadmap ensures sustainability and measurable return on investment:
Phase 1: Baseline assessment
Conduct a full energy audit of existing boiler systems: measure fuel consumption, heat transfer efficiency, and pollutant output (CO₂, NOₓ, SOₓ). Identify critical inefficiencies such as heat loss through exhaust, fuel underburn, steam leaks, or poor insulation.
Businesses may hire certified audit firms or engage with government-supported energy technical centers for assistance.
Phase 2: Technology selection
Based on audit results and operational needs:
- For SMEs: Choose compact boilers with built-in heat recovery (economizer, air preheater) or fluidized bed models.
- For food/pharma plants: Prioritize LNG boilers or oil-free clean steam systems to meet hygiene and safety standards.
- For large energy users: Consider CHP (Combined Heat & Power) systems – simultaneously generating electricity and steam for maximum efficiency.
Selection should balance technical performance, ROI, and legal compliance – especially for exporters.
Phase 3: Monetize emission reductions via Carbon Credits
After deployment, calculate emission reductions under ISO 14064. A reduction of 500–1,000 tCO₂e/year qualifies for local or international carbon markets.
Sell credits via domestic pilot exchanges or reputable global registries like Verra or Gold Standard.
Incorporate ESG reporting to boost credit rating, attract impact investors, and position for green IPOs.