Designing industrial pipelines requires selecting durable materials, carefully calculating pressure and temperature, adhering to international standards, and optimizing layout in limited spaces. These challenges demand creativity and the application of advanced technologies, promising safe and efficient design solutions. Let’s explore the detailed requirements and challenges in the content below.
1. Technical requirements in Pipeline Design
1.1. Material selection
Materials selection for pipeline systems in heavy industry is a strategic decision that directly affects the performance and durability of the entire system. Particularly in harsh environments such as the transportation of oil, gas, chemicals, and water, the material must ensure stability and resilience under severe conditions.
For example, when transporting oil or gas, the material must have high resistance to temperature and pressure, while also being able to withstand corrosion caused by chemical substances. Stainless steel, special alloys, or composite materials are commonly used to meet these requirements due to their high wear resistance and strength.
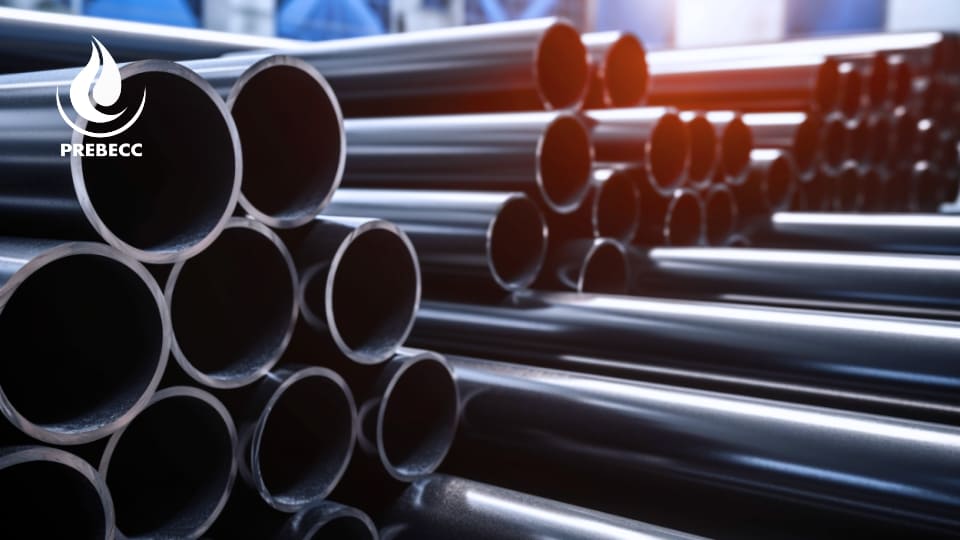
1.2. Operating Pressure and Temperature
Designing pipeline systems in heavy industrial environments requires careful calculations regarding the pressure and temperature that the system will endure throughout its operational life.
High pressure and extreme temperatures can cause thermal expansion and significant stress on the pipeline walls, leading to potential failures if not properly calculated. Stress analysis and the appropriate selection of wall thickness are crucial factors to ensure that the pipeline system can operate safely and efficiently throughout its lifespan.
For special applications, it may be necessary to employ design methods such as Finite Element Analysis (FEA) to simulate and optimize the load-bearing capacity of the pipeline.
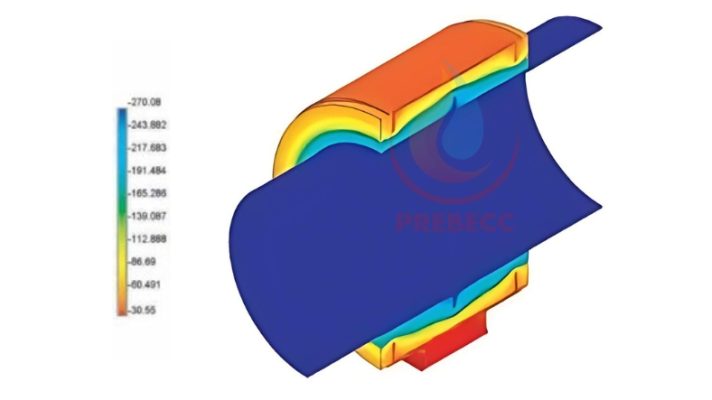
1.3. Standards and Technical Regulations
Compliance with standards and technical regulations is essential in the design of pipeline systems for heavy industry.
International standards such as those from ASME (American Society of Mechanical Engineers), ANSI (American National Standards Institute), and API (American Petroleum Institute) provide detailed guidelines on the design, manufacturing, installation, and inspection of pipelines.
These standards specifically address aspects such as Maximum Allowable Working Pressure (MAWP), wall thickness, and Non-Destructive Testing (NDT) methods to ensure maximum quality and safety. Adhering to these standards not only ensures that the pipeline system meets technical requirements but also helps minimize legal risks and protect the company’s reputation.
1.4. Safety and Maintenance
Safety is a top priority in the design of pipeline systems, especially in high-risk environments such as refineries, chemical plants, and other production facilities. The design must ensure that the pipeline system can withstand emergency situations such as leaks, explosions, or fires. This requires the integration of safety valves, pressure relief systems, and continuous monitoring devices to detect abnormalities early.
Regular maintenance is a crucial part of extending the lifespan of the pipeline system and maintaining operational efficiency. Maintenance procedures should include visual inspections, the use of advanced measurement tools to detect material degradation, and conducting pressure tests and non-destructive inspections.
A detailed maintenance plan, including schedules and appropriate maintenance methods, helps ensure that the pipeline system remains in optimal working condition while preventing potential failures.
2. Challenges in Pipeline Design
2.1. Terrain and Harsh Environmental Conditions
Designing pipelines in heavy industrial settings requires detailed calculations regarding the terrain and harsh environmental conditions that the system will face.
Complex terrains such as mountains, seabeds, and areas prone to earthquakes pose significant challenges for the installation and maintenance of pipelines. In these areas, seismic activity and landslides can cause deformation or breakage of the pipeline if not designed and installed correctly.
To address these challenges, techniques such as dynamic analysis and geological simulation are needed to ensure that the pipeline can withstand environmental impacts. Solutions like using elastic materials and designing flexible joints are also applied to minimize risks.
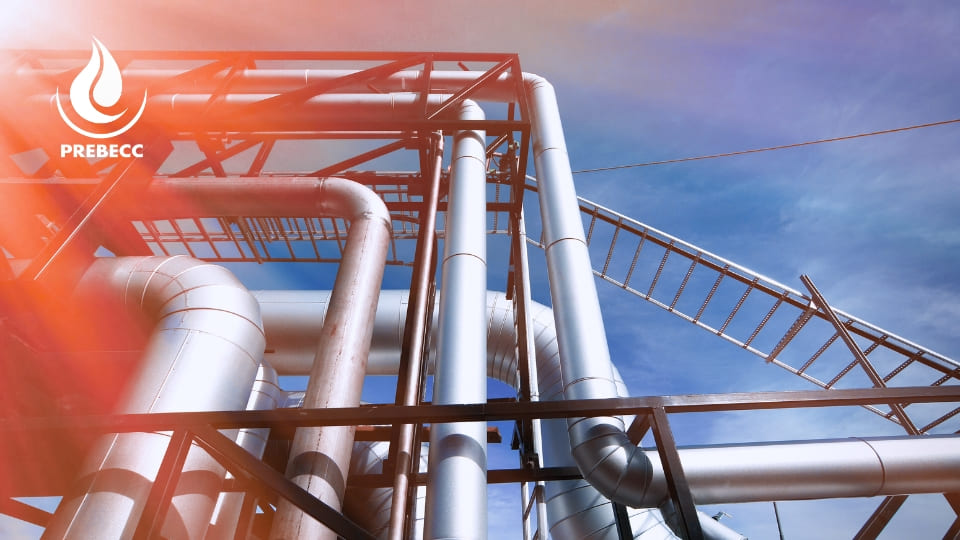
2.2. Site Management and Pipeline Layout
In factories and industrial zones, the installation space for pipelines is often limited due to the congestion of other equipment and systems.
Arranging pipelines in a confined space is a challenging task, requiring optimization of space while ensuring accessibility and ease of maintenance. Particularly when installing pipelines in areas with high equipment density, there is a significant risk of collisions and unwanted interactions between systems.
To address this issue, engineers often use 3D design software to simulate and plan the pipeline layout, allowing them to find the most optimal solution. Additionally, selecting reasonable pipeline routes and using accessories such as pressure relief valves and flexible joints can help minimize collisions and enhance system performance.
2.3. Integration with Other Systems
Pipeline design is not just about installing an isolated system; it must also be synchronized and integrated with other systems within the plant, including control systems, safety systems, and auxiliary systems. Ensuring that all these systems operate harmoniously and efficiently requires close collaboration between design and operation engineering teams.
One of the biggest challenges is maintaining the flexibility and scalability of the pipeline system while still meeting stringent safety and performance requirements. To solve this problem, engineers need to conduct system integration analyses and use modular design solutions, which allow for easy expansion and upgrades without disrupting plant operations.
3. New Solutions and Technologies
3.1. Simulation Design Technology (CAE/CAD)
As the heavy industry increasingly demands precision and efficiency, the application of simulation design technologies such as CAE (Computer-Aided Engineering) and CAD (Computer-Aided Design) has become a core element in the pipeline design process.
These advanced software tools allow engineers to simulate the entire pipeline system in a virtual environment, enabling them to evaluate and optimize the design before actual implementation.
One of the key benefits of simulation technology is the ability to perform Computational Fluid Dynamics (CFD) analysis, which helps predict fluid flow, pressure, and temperature within the pipeline with high accuracy. As a result, potential issues such as flow turbulence, hot spots, or excessive pressure can be identified and addressed during the design phase, ensuring stable and safe system operation.
3.2. New Materials and Welding Technologies
Material technology has always played a crucial role in enhancing the durability and performance of pipelines in heavy industry. Currently, new materials such as high-strength alloys with superior heat resistance and corrosion resistance are being researched and widely applied.
These materials not only extend the lifespan of pipelines but also reduce maintenance and replacement costs. Moreover, advanced welding technologies, such as laser welding and electron beam welding, are gradually replacing traditional welding methods.
These technologies offer higher precision, better mechanical strength for joints, and minimize the risk of defects due to welding. The combination of new materials and modern welding technologies ensures the integrity of pipeline systems even under the most severe operating conditions.
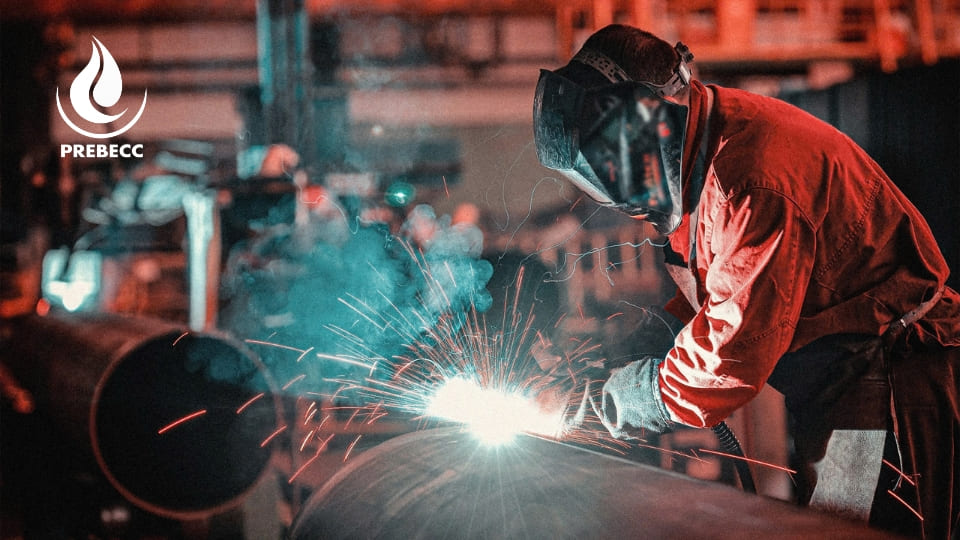
3.3. Intelligent Monitoring and Management
With the development of IoT (Internet of Things) technologies and remote monitoring, the management and maintenance of pipeline systems in heavy industry have entered a new era. Smart sensors installed along the pipeline allow real-time monitoring of the system’s operating conditions, from temperature and pressure to the condition of the joints.
Data collected from these sensors are analyzed and processed using Big Data tools, enabling managers to identify early signs of abnormalities and make timely maintenance decisions. Not only do intelligent monitoring solutions reduce the risk of incidents, but they also optimize operational costs and enhance the efficiency of the pipeline system. This technology is gradually becoming the standard in managing complex and large-scale pipeline systems.
4. Prebecc’s Pipeline Design Services
Prebecc is proud to be a leading provider of professional pipeline design services for heavy industry projects. With a team of experienced engineers who possess deep knowledge of international technical standards, we are committed to delivering the most optimal, safe, and efficient design solutions to our clients.
4.1. Optimized design process
At Prebecc, we employ a rigorous pipeline design process, starting from on-site surveys, evaluating client requirements, to selecting appropriate materials and technologies. Each step is carried out with the utmost care and precision to ensure that the pipeline system meets all technical requirements and safety standards.
4.2. Application of modern technologies
We utilize advanced design technologies such as CAD/CAE and Computational Fluid Dynamics (CFD) analysis to simulate and optimize the design. This not only minimizes risks but also enhances the performance and lifespan of the pipeline system under harsh operating conditions.
4.3. Professional engineering team
Prebecc’s engineering team is not only highly experienced in the heavy industry but also thoroughly trained in international standards and regulations such as ASME, API, and other industry-specific codes.
This extensive expertise allows us to design pipeline systems that meet all technical requirements and deliver the highest operational efficiency for our clients.
4.4. Comprehensive customer support
Our services extend beyond design to include support throughout construction, installation, and maintenance. We are always ready to provide advice and answer any questions from our clients, ensuring that the pipeline system is implemented in the most perfect and sustainable way.
At Prebecc, each pipeline design project is a commitment to quality, safety, and the absolute satisfaction of our clients. Contact us today to receive the most professional and reliable pipeline design solutions in the heavy industry.