Recent updates in design and technology have led to the development of more efficient boilers that require less maintenance compared to conventional versions. However, for businesses and manufacturing facilities not yet ready to replace their boilers, proper operation and maintenance are crucial to maximizing efficiency. This translates to cost savings through reduced energy consumption and, in some cases, reduced chemical use. Particularly, it helps in lowering air pollutants, specifically NOx or nitrogen oxides, a byproduct of the combustion process.
1. Improving combustion processes
1.1 Adjusting air supply ratio:
The air supply ratio in the combustion process is known as the excess air coefficient. If this coefficient is too high, it wastes fuel and increases NOx emissions. On the other hand, if it’s too low, incomplete combustion occurs, leading to higher CO emissions and unburned organic compounds.
Solutions:
- Use of Measurement Devices: Equip modern measuring devices like gas analyzers to continuously monitor O2 levels in exhaust gases.
- Adjusting Air Supply Flow: Adjust the air supply flow based on measurement results to achieve the optimal air ratio.
- Optimizing the Air Supply System: Regularly inspect and adjust the air supply system to ensure even air distribution in the combustion chamber.
- Implementing Automatic Control Technology: Use automated control systems to accurately and continuously adjust the air supply flow.
- Automatic Combustion Control System: Modern automatic control systems can continuously monitor combustion parameters such as temperature, pressure, and air/fuel ratio. By automatically adjusting the air supply, these systems help optimize combustion efficiency and reduce heat loss.
- O2 Trim Control Technology: By using oxygen sensors, the control system can monitor the excess oxygen in the exhaust gases, thereby adjusting the air supply to achieve the precise ratio, avoiding excess or deficiency of air.
1.2. Using high-quality fuel:
Fuel quality directly affects the combustion process and emissions. Fuel with low sulfur and ash content will help reduce SOx emissions and dust, as well as minimize the corrosion of heat exchange surfaces.
Solutions:
- Selecting suitable fuel: Choose fuel with low sulfur and ash content, appropriate for the boiler’s design.
- Regular fuel quality checks: Conduct regular checks on fuel quality to ensure it meets technical standards.
- Fuel treatment: If necessary, implement fuel treatment measures to reduce sulfur and ash content before feeding it into the boiler.
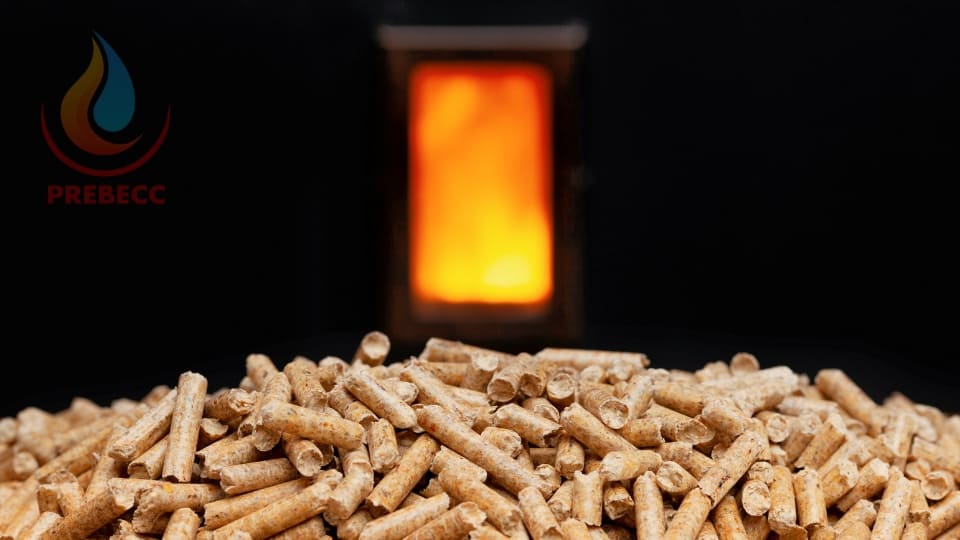
1.3. Controlling combustion chamber temperature:
A low combustion chamber temperature will lead to incomplete combustion, resulting in higher CO emissions and unburned organic compounds. Conversely, a temperature that’s too high will increase NOx formation.
Solutions:
- Adjusting fuel flow: Adjust the fuel flow to maintain a stable combustion chamber temperature.
- Controlling excess air: Adjust the excess air amount to ensure complete combustion without generating excessive NOx.
- Adjusting primary and secondary airflow: Primary airflow helps maintain an appropriate combustion chamber temperature to ensure complete fuel combustion. Secondary airflow helps cool exhaust gases before they exit to the environment, reducing NOx and SOx formation.
- Cooling systems: Cooling systems can be integrated to control the combustion chamber temperature, especially when burning fuels that tend to generate high temperatures. Maintaining the temperature at an optimal level helps minimize NOx formation without reducing combustion efficiency.
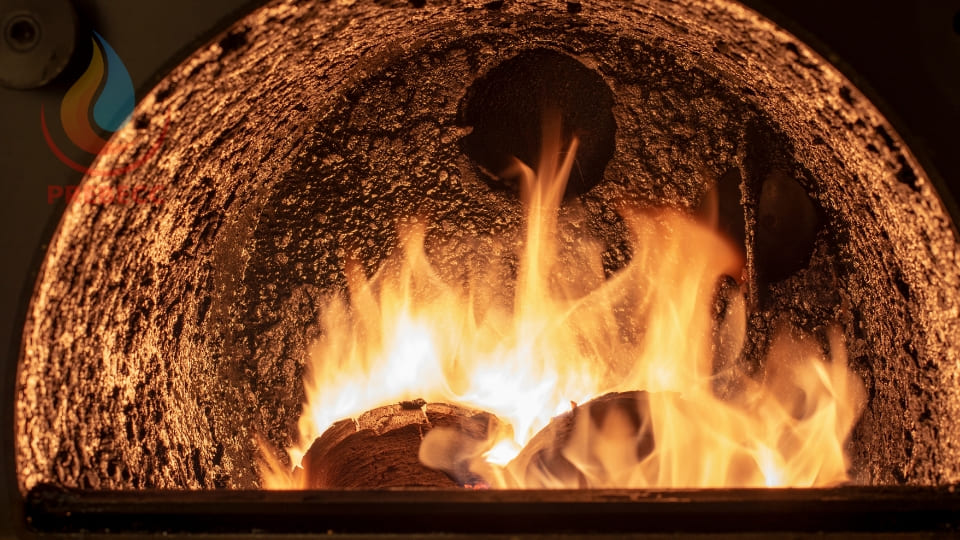
1.4. Other solutions:
- Advanced Combustion Technologies: Implement advanced combustion technologies such as fluidized bed combustion, circulating fluidized bed combustion, and low NOx combustion to reduce emissions.
- Optimizing Combustion Chamber Design: Design the combustion chamber to facilitate complete combustion and minimize NOx formation.
- NOx Reduction Systems: Equip NOx reduction systems like SCR (Selective Catalytic Reduction) or SNCR (Selective Non-Catalytic Reduction) to reduce NOx emissions in exhaust gases.
2. Regular boiler cleaning
Regular boiler cleaning and maintenance are key factors in ensuring stable operation, high efficiency, and emission reduction. According to experts, boilers are subject to significant impacts from high temperatures and pressures, so if not properly maintained, issues such as corrosion, scaling, and leakage can occur, leading to reduced operational efficiency and increased operating costs. Notably, neglecting regular boiler cleaning can result in dirt buildup, reducing heat transfer efficiency, increasing fuel consumption, and raising harmful emissions.
2.1. Cleaning heat exchange surfaces
Heat exchange surfaces in boilers, including steam pipes and combustion chamber surfaces, must be kept clean to ensure optimal heat transfer efficiency. When these surfaces are scaled or dirty, heat transfer is impeded, leading to increased fuel consumption and reduced thermal efficiency of the boiler.
Solutions:
- Steam or Chemical Cleaning: Experts recommend using high-pressure steam cleaning or specialized chemicals to remove scale and dirt from heat exchange surfaces.
- Mechanical Cleaning: In cases where dirt is difficult to remove, boiler maintenance teams can use mechanical devices such as brushes or ultrasonic cleaners to clean the internal surfaces of the boiler.
2.2. Inspecting and Maintaining the fuel combustion system
The fuel combustion system is the heart of the boiler, determining combustion efficiency and emission levels. Regular maintenance of this system ensures that the combustion process is optimal, with fuel being fully burned, minimizing CO and NOx emissions.
Solutions:
- Inspecting and Adjusting Fuel Nozzles: Fuel nozzles should be regularly inspected and adjusted to ensure the air/fuel ratio is always optimal.
- Cleaning and Replacing Worn Parts: Components like fuel nozzles and pipes should be cleaned and replaced as needed to ensure the fuel combustion system operates smoothly.
2.3. Inspecting and treating boiler feed water
Boiler feed water can contain impurities such as sediments, minerals, and dissolved gases, leading to scaling and corrosion inside the boiler. Regularly inspecting and treating feed water helps prevent these issues, extending the boiler’s life and reducing maintenance costs.
Solutions:
- Filtration and De-mineralization Systems: Filtration and de-mineralization systems help remove harmful impurities in the feed water, preventing scaling in the boiler.
- Monitoring and Adjusting pH Levels: Ensure the feed water has an appropriate pH level to avoid corrosion of metal surfaces inside the boiler.
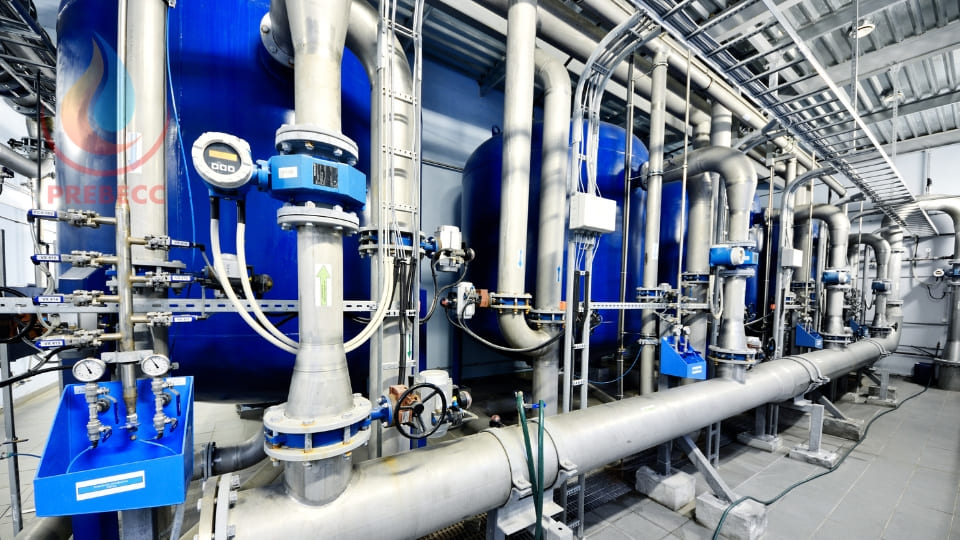
2.4. Inspecting and maintaining blowdown and venting systems
Blowdown and venting systems play a critical role in removing sediments and unwanted gases from the boiler, helping maintain water quality and operational efficiency.
Solutions:
- Inspecting and Cleaning Blowdown Valves: Blowdown valves should be regularly inspected and cleaned to ensure effective operation, prevent blockages, and ensure complete sediment removal.
- Maintaining Venting Systems: Venting systems should be inspected to ensure there is no buildup of unwanted gases, helping to maintain stable pressure and temperature within the boiler.
3. Operation management
3.1. Monitoring operational parameters:
Monitoring operational parameters is the first and most crucial step in managing a boiler. Continuously monitoring indicators such as steam pressure, feed water temperature, fuel flow, and exhaust gas temperature allows operators to detect early signs of abnormalities, enabling timely intervention before severe issues arise.
Detailed Analysis:
- Steam Pressure: Steam pressure is one of the most critical parameters of the boiler, directly affecting the system’s efficiency and safety. If steam pressure exceeds the allowable threshold, there is a risk of boiler explosion, while too low pressure will reduce the boiler’s efficiency.
- Feed Water Temperature: Monitoring feed water temperature ensures efficient steam generation. Too cold feed water can reduce boiler efficiency and increase fuel consumption, while too hot feed water can cause abnormal boiling and affect system safety.
- Fuel Flow: Measuring the fuel flow supplied to the boiler helps control the combustion process and optimize thermal efficiency. Abnormal changes in fuel flow may indicate technical issues or fuel loss.
- Exhaust Gas Temperature: Exhaust gas temperature is a crucial indicator for evaluating combustion efficiency. Too high exhaust gas temperature may indicate energy waste, while too low temperature may signal inefficiency in the combustion process.
3.2. Utilizing automatic control systems:
Automatic control systems offer many outstanding benefits in boiler operation management, including the ability to optimize combustion processes, minimize human error, and enhance overall system efficiency:
- Automated Adjustments: Automatic control systems allow for precise and continuous adjustments of operational parameters such as pressure, temperature, and fuel flow based on real-time data, maintaining the boiler’s performance at an optimal level.
- Continuous Monitoring: Automatic control systems can continuously monitor the technical parameters of the boiler and provide early warnings when abnormal signs are detected, helping prevent issues before they become serious.
- Minimizing Human Error: One of the most significant benefits of automatic control systems is the reduction of human error, such as incorrect parameter adjustments or missed important tasks. This not only enhances safety but also improves operational efficiency.
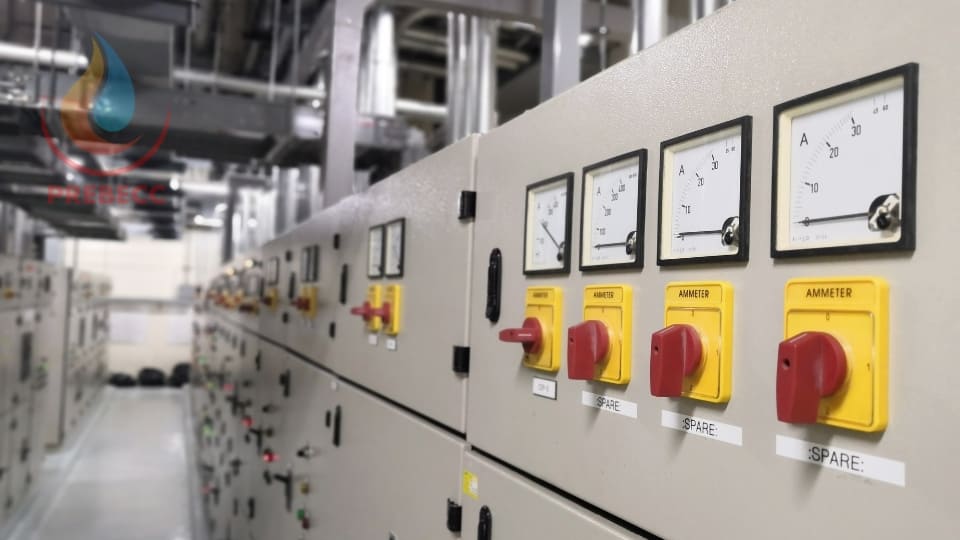
Example:
Implementing SCADA (Supervisory Control and Data Acquisition): The SCADA system is an effective operation management solution, allowing remote monitoring and control of equipment within the boiler. This system provides detailed data on the boiler’s operational performance, enabling management to make optimized operation decisions.
Integrating IoT (Internet of Things) Technology: Integrating IoT technology into the boiler system helps collect data from various sensors and devices, providing detailed information on operational status and early warnings of potential issues.
3.3. Training and skill development for operating staff
The boiler operation team is responsible for daily adjustments and monitoring. Their skills and knowledge play a crucial role in ensuring efficient and safe boiler operation. Training employees on operation procedures, maintenance, and troubleshooting not only enhances performance but also reduces safety and environmental risks.
Solutions:
- Regular Training Programs: Companies should organize regular training sessions on boiler operation and maintenance skills, as well as updates on new technologies and methods in the industry.
- Detailed Operation Manuals: Provide detailed manuals on operation procedures and troubleshooting to help employees carry out tasks accurately and safely.
- Hands-on Practice: Practical experience is the best way for operators to understand the boiler system and learn how to adjust operational parameters in real-world situations.
As energy efficiency and environmental protection requirements increase, efficient boiler operation and emission reduction have become critical tasks for every business.
With years of experience in the boiler industry, Prebecc Company Limited not only offers design and manufacturing consultancy solutions but also specializes in project management, training, and maintenance services. Prebecc’s comprehensive services help clients optimize boiler performance, minimize operational costs, and meet the most stringent environmental standards.