There are many reasons why regular boiler inspections are overlooked during operation, which poses significant risks to businesses in terms of safety and assets.
1. Boiler Operation and Inspection
Operating a boiler requires meticulousness and high precision. To ensure the boiler operates stably, safely, and efficiently, several crucial tasks must be performed.
Daily tasks during boiler operation include:
- Continuously monitoring parameters: Boiler pressure, boiler temperature, exhaust gas temperature, feed water pressure and temperature…
- Inspecting the system: Burners, control valves, feedwater tanks, deaerators, water treatment systems…
- Sampling water: Comparing with standards to ensure feed water quality.
Manufacturers often provide detailed maintenance schedules for each type of boiler. Adhering to this schedule is extremely important because it helps:
- Early detection of problems: Through regular inspections, we can identify and promptly address minor defects before they lead to serious consequences.
- Ensuring performance: Regular maintenance helps the boiler operate stably, minimizes fuel consumption, and extends its lifespan.
- Ensuring safety: Neglecting maintenance can lead to dangerous incidents such as boiler explosions, toxic gas leaks…
An operation log is an indispensable tool for monitoring and analyzing the boiler’s performance. Thorough recording of operating parameters, inspection results, and incidents helps us build a detailed database, enabling precise decisions to optimize operation and maintenance processes.
Boiler maintenance is a critical task that cannot be overlooked. Proper and thorough execution of maintenance tasks will help prolong the boiler’s lifespan, ensure production safety, and minimize operating costs.
2. Why Boiler Inspections Are Often Overlooked
There are many reasons why regular inspections and maintenance are overlooked during boiler operation, but lack of training and cost-cutting pressures are the two main reasons why many businesses neglect regular boiler maintenance.
One of the primary reasons many businesses overlook regular boiler maintenance is due to inadequate training for staff. When employees are not adequately equipped with the knowledge and awareness of the importance of maintenance, combined with economic difficulties, maintenance activities are often undervalued.
To address the issue of expertise in boiler operation, many places have implemented boiler operator training and certification programs to ensure that only experienced and knowledgeable staff operate boilers in their areas.
However, under the pressure of competition and the need to cut costs, many businesses even skip the expenses for operational training and regular maintenance. In the short term, cutting the maintenance budget may provide immediate savings, but in the long term, it results in unforeseeable consequences. Not conducting regular maintenance will lead to rapid equipment deterioration, increased repair costs, and potentially significant production losses.
While training may seem like an unnecessary expense, proper training and maintenance will save money for the owners through efficient operation, incident prevention, and avoiding production interruptions. The cost of hiring trained and licensed personnel will extend the lifespan of valuable equipment while maintaining its safe and efficient operation.
Prebecc Company is trusted as a regular boiler inspection partner for many businesses.
Moreover, given the inherent dangers of boiler systems (especially high-capacity boilers according to ASME Section I standards), regular maintenance should not be neglected.
3. Some risks of not conducting regular boiler inspections and maintenance
Regular inspection of safety devices (LWCO, ALWCO, safety valves, gas/fuel line valves, etc.) is the first line of defense against major failures. Although these devices are inspected during annual checks by regulatory agencies or insurance companies, once a year is not sufficient. All these devices should be regularly inspected and tested to avoid any issues. Neglecting the maintenance of these safety devices exposes you to inherent risks associated with pressure vessels.
Monitoring boiler operating pressure and temperature, along with flue gas temperature, helps operators promptly detect system issues. If boiler pressure frequently exceeds the set limit, this may indicate a problem with the control switch.
If the boiler’s flue gas temperature is consistently 50°-100°F higher than the steam temperature, this may indicate the need to adjust combustion and inspect the boiler for scaling. Scaling reduces heat transfer efficiency and can cause tube failures. When daily maintenance checks are not performed, minor signs of inefficient operation and internal scaling will be overlooked.
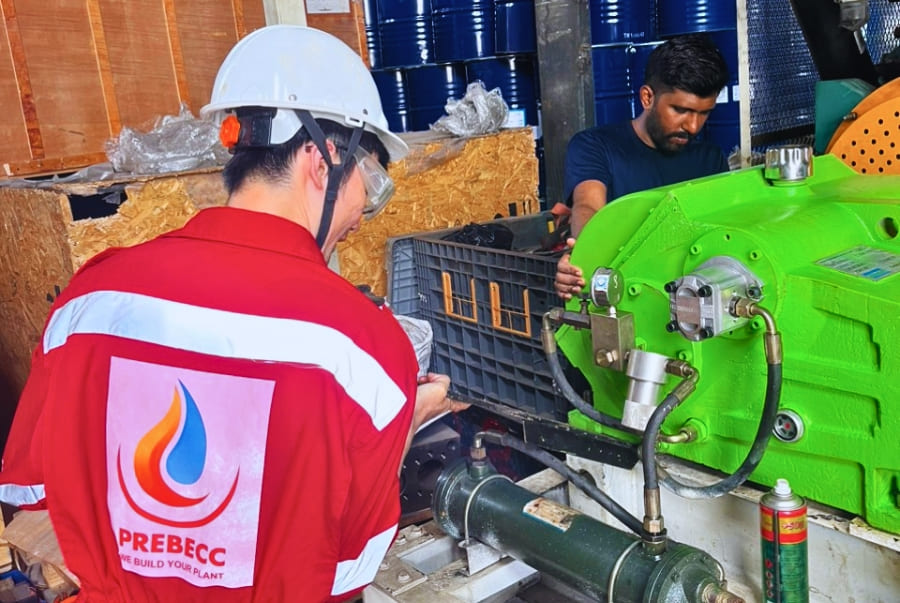
Monitoring feedwater pressure and temperature helps operators recognize abnormal trends in the feedwater system. If pressure or temperature deviates from the normal range, feedwater may not enter the boiler or cause damage due to thermal shock. When there is a large temperature difference between feedwater and boiler water, the boiler will be affected by “thermal fatigue.”
This starts at the feedwater joints and can develop into cracks spreading to the boiler shell. Depending on the operating pressure and temperature, these cracks can lead to hazardous fluid and steam leaks, posing a risk of injury to operating personnel.
Observing the flame through the sight glass is a simple way to detect early signs of adjustment issues or damage before they become major concerns. Ignoring this inspection can lead to inefficient combustion and potential boiler system failure.
While most boiler explosions familiar to people are related to water level issues, combustion chamber explosions are also a significant concern. Regularly inspecting the sight glass and gas/fuel lines will minimize risks associated with the combustion process.
Regular inspection of water treatment equipment and frequent water sampling help ensure that no issues related to water treatment and supply are overlooked. Neglecting these inspections can result in inefficient, improper, or unsafe boiler operation, leading to component failures.
Infrequent blowdown or neglecting it during boiler operation will increase the concentration of impurities, contributing to scaling, corrosion, and other operational issues. Failure to maintain boiler water chemistry as recommended by the manufacturer will result in severe failures, including boiler tube overheating, metal corrosion, and steam line erosion.
When many maintenance tasks are overlooked, issues will accumulate and lead to significant boiler system failures. Neglecting boiler maintenance not only puts operating personnel at risk but also results in premature failure of components and equipment, costing the company due to inefficient operation, downtime, repairs, and replacements. To mitigate these risks, adhere to the recommended guidelines for all routine maintenance tasks.