A water-tube boiler is one of the most common and efficient types of industrial boilers today—especially suited for systems requiring high steam pressure and large capacity, such as thermal power plants, food processing facilities, chemical plants, textile dyeing factories, and other heavy industries. The key distinction between water-tube and fire-tube boilers lies in the flow configuration of water and hot gases. In a water-tube boiler, water flows inside the tubes while hot gases circulate outside them.
1. Operating principle of Water-Tube Boilers
The operating principle of a water-tube boiler is based on heat exchange between hot gases generated from fuel combustion and the water flowing inside heat-resistant steel tubes. The process involves:
Fuel combustion to generate heat
Fuels such as oil, natural gas, coal, or biomass are combusted in the furnace, producing high-temperature flue gases. In modern combustion systems, the burning process is regulated by forced-draft air supply and optimized fuel–air ratio control to improve thermal efficiency.
Water circulation through the tubes
Feedwater enters the system via an economizer and then flows through generating tubes arranged around the furnace or in high-temperature zones. Heat from the flue gases transfers through the tube walls, boiling the water and forming a steam-water mixture.
Steam generation and collection
Steam is collected in the steam drum, where water and steam separation occurs. Water that is not fully evaporated is recirculated, while the saturated steam may pass through a superheater to increase its temperature—producing superheated steam suitable for turbines or production lines requiring high thermal energy.
The entire system operates as a closed circulation loop, either through natural circulation (driven by density differences between hot and cold water) or forced circulation (using pumps to maintain consistent flow and pressure).
2. Main components and functions of a Water-Tube Boiler
Water-tube boilers are designed and manufactured in accordance with strict standards to ensure maximum safety and operational efficiency. Each component plays a crucial role not only in steam generation and transport but also in system protection, control, and heat transfer optimization. Below are the core components and their functions:
2.1. Furnace
The furnace is the central combustion chamber where fuel is burned. It is constructed using high-temperature-resistant materials—typically alloy steel or lined with refractory bricks—to withstand intense heat and corrosive combustion by-products.
- Primary function: Provide an optimal combustion environment to generate high heat for water heating.
- Technical requirements: Ensure even heat distribution, minimize hot spots, and maintain complete combustion to meet emissions standards.
2.2. Heating surfaces
These include all areas where heat transfer occurs from the hot gases to the water, typically comprising the following elements:
a. Generating Tubes
Location: Surround the furnace or placed in high-temperature zones.
Function: Contain water and absorb heat to generate saturated steam. These tubes are made of high-pressure-resistant steel, with dimensions calculated precisely to industry standards.
→ Explore EN 12952 design standards for water-tube boilers
b. Superheater
Function: Increases the temperature of saturated steam after it leaves the steam drum, creating superheated steam for turbines or equipment that requires dry, high-temperature steam.
Design: Typically U-shaped horizontal tubes positioned in the hottest flue gas zone downstream of the furnace.
c. Economizer
Location: Near the end of the flue gas path, just before the stack.
Function: Recovers residual heat from flue gases to preheat feedwater entering the steam drum, reducing fuel consumption.
d. Air Preheater (if applicable)
Function: Uses flue gas heat to warm combustion air before it enters the furnace, improving combustion efficiency and reducing flue gas temperature.
Common types: Tubular or rotary air preheaters.
2.3. Steam Drum
The steam drum is the key component where the phase separation between steam and water occurs. It plays a critical role in stabilizing steam quality and protecting downstream steam-consuming equipment.
Main functions:
- Collects the steam-water mixture from the evaporator tubes.
- Performs moisture separation using mechanical steam separators.
- Redistributes circulating water back into the steam-generating tubes.
- Houses important devices such as water level sensors, safety valves, and measurement instruments.
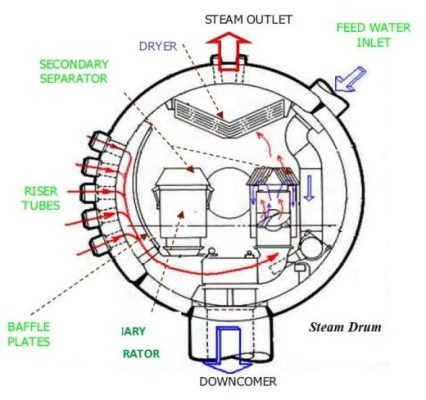
2.4. Feedwater System
This system includes the feedwater pump, piping, and water treatment units (filtration, deaeration, demineralization, etc.).
Function: Ensures the supply of clean, stable, and properly pressurized water into the system, preventing boiler drum dry-out or corrosion caused by poor-quality water.
2.5. Ash and Slag Removal System (for coal or solid fuel-fired boilers)
Function: Collects and removes ash and slag after combustion, maintaining the cleanliness of the furnace and heat exchange surfaces.
Common types:
- Dry ash removal systems: typically include screw conveyors or belt conveyors.
- Wet ash removal systems: use water to cool and transport ash, helping to reduce dust emissions.
- These systems can be operated manually or automatically depending on the boiler design.
2.6. Control and Safety System
Includes:
- Temperature, pressure, and flow sensors.
- PLC or DCS-based automated control systems.
- Safety devices such as safety valves, pressure switches, high/low water level alarms, and load controllers.
Function: Ensures safe and optimized operation of the boiler, preventing issues such as overpressure, low water level, overheating, or backfiring.
3. Classification of Water-Tube Boilers based on different criteria
Water-tube boilers are flexibly designed to meet various usage demands and operating conditions. Depending on structural features, operating principles, and installation configurations, water-tube boilers can be classified as follows:
3.1. Classification by tube structure: Straight Tube and Bent Tube
a. Straight Tube Water-Tube Boiler
- Structure: Water tubes are arranged vertically or at an incline, connecting the steam drum and mud drum.
- Advantages: Simple design, easy to fabricate and clean internal scale.
- Applications: Suitable for systems with moderate steam flow requirements and frequent maintenance needs.
b. Bent Tube Water-Tube Boiler
- Structure: Water tubes are bent to increase heat transfer area and improve circulation flow.
- Advantages: Flexible layout, greater exposure to hot gases, higher heat transfer efficiency, ideal for high-capacity systems.
- Applications: Common in power plants and heavy industrial facilities requiring high-pressure and high-capacity steam.
3.2. Classification by Water Circulation Method: Natural and Forced Circulation
a. Natural Circulation Boiler
- Principle: Water circulates due to the density difference between hot and cold water in the tubes.
- Advantages: No need for a circulation pump, simple design, low power consumption.
- Limitations: Limited in rapid load increase, harder to control water flow precisely.
- Applications: Typically used in small to medium industrial steam systems.
b. Forced Circulation Boiler
- Principle: A pump forces water through the heat exchange tubes.
- Advantages: Precise control of water flow, suitable for rapidly changing loads, meets high steam output requirements.
- Limitations: Higher investment and operating costs, requires regular maintenance of the circulation pump.
- Applications: Thermal power plants, steam turbine systems, high-stability process applications.
3.3. Classification by Number of Steam Drums: Single Drum and Bi-Drum
a. Single Drum Boiler
- Features: All steam separation and water recirculation take place in one drum.
- Advantages: Compact design, easier installation and maintenance, reduced equipment cost.
- Limitations: Less effective at handling large loads compared to bi-drum types.
- Applications: Medium and small industrial plants with moderate steam demands.
b. Bi-Drum Boiler
- Features: One steam drum at the top and one mud drum at the bottom, connected by convection tubes.
- Advantages: Improved water circulation efficiency, better steam-water phase separation, more stable under fluctuating load conditions.
- Limitations: More complex structure, higher manufacturing and installation costs.
- Applications: Power generation units, large-capacity boilers, thermal power stations.
3.4. Classification by Overall Structural Shape: D-type, O-type, A-type
This classification is based on the Latin letter shape formed by the layout of steam drums, water tubes, and the furnace.
a. D-Type Boiler
Configuration: Features one steam drum on top and one mud drum below, with water tubes bent into a “D” shape when viewed from the side.
Key characteristics:
- The furnace is offset to one side.
- Compact design, space-saving in width.
- Suitable for applications requiring high capacity and operational stability.
Applications: Power plants, marine vessels, and large-scale industrial steam systems.
Advantages: Easy maintenance, efficient steam-water separation, rapid response to load changes.
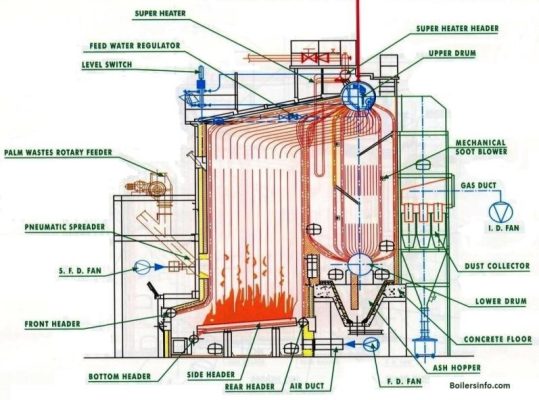
b. O-Type Boiler
Configuration: Comprises two drums – one on top and one on the bottom – arranged vertically and symmetrically. Water tubes surround the centrally located furnace in a circular or elliptical layout (resembling the letter “O” when viewed from the side).
Key characteristics:
- The furnace is positioned in the center, fully enclosed by water tubes.
- Symmetrical design ensures balanced heat distribution.
- Well-suited for continuous operation systems requiring high reliability.
Advantages:
- Minimizes thermal stress imbalance, stable operation.
- Easy to upgrade the combustion system and heat recovery components.
c. A-Type Boiler
Configuration: Features one steam drum at the top and two mud drums at the bottom sides (forming the legs of the “A” shape), connected to the steam drum via slanted water tubes.
Key characteristics:
- Optimized for vertical space; furnace located between two angled tube banks.
- Capable of operating under high pressure, suitable for large and continuous steam loads.
- Applications: Oil refineries, petrochemical industries, and energy systems with high-pressure steam requirements.
Classifying boilers by D, O, and A-type configurations helps engineers select a suitable layout based on installation space, operating characteristics, and system capacity requirements. This classification is also a critical factor in custom-designed boilers and large-scale EPC projects.
Contact for design and manufacture of water tube boilers
Hotline: (+84) 7 08 09 1033
Email: info@prebecc.com
With experienced engineers and strong design and manufacturing capabilities, we are confident in meeting a series of the most stringent standards in the boiler and pressure equipment industry such as:
- ASME Section I, ASME Section VIII Div.1 & Div.2
- ASME B31.1, API-650, API-620
- EN-12952, EN-12953, EN-13445, EN-13480
- PED 2014/68/EU, KSB 6753, EN-1090, EN-3834, TCVN 12728, EN-1990
From detailed design to manufacturing and installation, Prebecc is committed to providing safe, efficient and optimal boiler systems for each use.