Trong ngành công nghiệp nặng, thiết bị áp lực đóng vai trò quan trọng trong việc chứa, vận chuyển và xử lý môi chất ở áp suất cao. Tuy nhiên, một trong những thách thức lớn nhất trong thiết kế là tải trọng phức tạp – yếu tố ảnh hưởng trực tiếp đến độ bền, an toàn và tuổi thọ của thiết bị.
Làm thế nào để đảm bảo thiết bị có thể chịu được tác động đồng thời của áp suất, nhiệt độ, ứng suất dư và tải trọng bên ngoài mà không gây mất ổn định kết cấu? Câu trả lời nằm ở việc áp dụng phương pháp thiết kế hiện đại, tối ưu hóa vật liệu và tuân thủ các tiêu chuẩn kỹ thuật nghiêm ngặt như ASME BPVC Section VIII, EN 13445 và API 579.
1. Tải trọng phức tạp trong thiết kế thiết bị áp lực
Tải trọng phức tạp trong thiết bị áp lực là sự tổng hợp của nhiều loại lực tác động đồng thời, không chỉ giới hạn ở áp suất làm việc mà còn bao gồm tải trọng cơ học, nhiệt, động và ứng suất dư. Không giống như tải trọng đơn giản, tải trọng phức tạp thường có tính phi tuyến, biến thiên theo thời gian và có thể gây ra các hiện tượng như ứng suất tập trung, mỏi vật liệu và mất ổn định kết cấu.
Thiết bị áp lực có thể chịu tác động từ nhiều nguồn tải trọng khác nhau, bao gồm:
- Áp suất bên trong và bên ngoài: Yếu tố chính tạo ra ứng suất màng trong vỏ thiết bị. Khi chênh lệch áp suất lớn, nguy cơ mất ổn định hoặc nổ vỡ có thể xảy ra nếu thiết kế không đủ độ bền.
- Nhiệt độ làm việc: Sự thay đổi nhiệt độ giữa các vùng khác nhau của thiết bị có thể tạo ra ứng suất nhiệt, làm tăng nguy cơ nứt do giãn nở không đồng đều.
- Lực tác động từ môi trường bên ngoài: Tải trọng gió, địa chấn, rung động từ thiết bị vận hành xung quanh có thể làm suy yếu khả năng chịu lực của thiết bị.
- Ứng suất dư từ quá trình chế tạo: Quá trình hàn, gia công nguội, hoặc xử lý nhiệt có thể để lại ứng suất dư trong vật liệu, làm giảm độ bền mỏi của thiết bị.
Một trong những vấn đề lớn nhất khi tính toán thiết bị áp lực là khả năng dự đoán chính xác sự kết hợp của các tải trọng trong suốt vòng đời vận hành. Nếu chỉ tính toán riêng lẻ từng loại tải mà không xem xét sự tương tác của chúng, thiết bị có thể bị quá tải cục bộ, dẫn đến hỏng hóc sớm.
Ngoài ra, các tiêu chuẩn thiết kế như ASME BPVC Section VIII và EN 13445 đưa ra những yêu cầu khắt khe về kiểm tra ứng suất, phân tích mỏi và đánh giá rủi ro để đảm bảo thiết bị có thể hoạt động an toàn dưới điều kiện tải trọng thực tế.
2. Các loại tải trọng tác động lên thiết bị áp lực
Thiết bị áp lực trong quá trình vận hành chịu nhiều loại tải trọng tác động đồng thời, có thể chia thành các nhóm chính sau:
Loại tải trọng | Nguyên nhân | Ảnh hưởng đến thiết bị |
---|---|---|
Tải trọng do áp suất bên trong | Áp suất làm việc từ chất lỏng hoặc khí nén bên trong thiết bị | Gây giãn nở thành thiết bị, tạo ứng suất kéo trong vật liệu |
Tải trọng do áp suất bên ngoài | Áp suất tác động từ bên ngoài (ví dụ: chân không, thiết bị làm việc dưới nước sâu) | Gây ứng suất nén, có thể dẫn đến hiện tượng ổn định kết cấu (buckle) |
Tải trọng nhiệt (Thermal Load) | Sự giãn nở hoặc co rút của vật liệu khi nhiệt độ thay đổi | Gây ứng suất nhiệt, có thể tạo nứt gãy hoặc cong vênh |
Tải trọng động (Dynamic Load) | Dao động áp suất, dòng chảy xoáy, rung động từ máy móc | Gây mỏi vật liệu, làm giảm tuổi thọ thiết bị |
Tải trọng cơ học (Mechanical Load) | Trọng lượng thiết bị, tác động từ giá đỡ, lực tác động bên ngoài | Tạo ứng suất tập trung tại mối hàn, điểm tiếp xúc |
Tác động hóa học (Chemical Load) | Ăn mòn do môi chất bên trong hoặc môi trường bên ngoài | Gây suy giảm độ bền vật liệu, xuất hiện rỗ ăn mòn hoặc nứt do ăn mòn ứng suất |
Tải trọng môi trường (Environmental Load) | Gió, sóng biển, động đất, chấn động từ các thiết bị xung quanh | Làm thiết bị rung lắc, có nguy cơ dịch chuyển hoặc phá hủy kết cấu |
3. Phân tích tải trọng áp suất bên trong và bên ngoài của thiết bị áp lực
3.1. Áp suất bên trong
Áp suất bên trong là yếu tố quan trọng nhất trong thiết kế thiết bị áp lực. Khi áp suất tăng, ứng suất sinh ra trong thành thiết bị tăng theo tỷ lệ thuận. Theo lý thuyết của Lame, ứng suất vòng trong thành ống chịu áp suất bên trong có thể được tính theo công thức:
Trong đó:
- P là áp suất bên trong,
- r là bán kính trung bình của thiết bị,
- t là chiều dày thành thiết bị.
Tuy nhiên, khi thiết bị có kết cấu phức tạp hoặc chứa các chi tiết gia cường như gân tăng cứng, bích nối, ứng suất tập trung có thể xuất hiện, đòi hỏi phải có các phân tích chi tiết hơn bằng phương pháp phần tử hữu hạn (FEA).
3.2. Áp suất bên ngoài
Khác với áp suất bên trong, áp suất bên ngoài tác động lên thiết bị áp lực theo hướng ép vào, có thể dẫn đến mất ổn định kết cấu (buckling) nếu không được thiết kế đúng tiêu chuẩn.
Khi áp suất bên ngoài tăng, vỏ thiết bị có xu hướng bị biến dạng đàn hồi, nhưng nếu vượt quá giới hạn, nó có thể gây ra biến dạng dẻo cục bộ, thậm chí sụp đổ hoàn toàn (collapse failure). Hiện tượng này thường xảy ra ở các thiết bị có thành mỏng như bình chân không, thiết bị làm việc trong môi trường áp suất thấp hoặc có tải trọng từ môi trường xung quanh như nước biển, đất đá.
Theo tiêu chuẩn ASME Boiler and Pressure Vessel Code (BPVC) Section VIII, Division 1, khả năng chịu áp suất bên ngoài của thiết bị được xác định dựa trên:
- Độ dày thành thiết bị: Càng mỏng, nguy cơ mất ổn định càng cao.
- Bán kính thiết bị: Bình có đường kính lớn dễ bị biến dạng hơn.
- Độ bền của vật liệu: Các vật liệu có mô đun đàn hồi cao chịu áp suất ngoài tốt hơn.
- Gia cường kết cấu: Gân tăng cứng hoặc vòng gia cường giúp thiết bị chịu tải tốt hơn.
Ngoài các tính toán lý thuyết, phân tích phần tử hữu hạn (FEA) thường được sử dụng để đánh giá chính xác nguy cơ mất ổn định, đặc biệt với thiết bị có hình dạng phức tạp hoặc làm việc trong điều kiện khắc nghiệt.
4. Tải trọng nhiệt và nguy cơ nứt giòn của thiết bị áp lực
Khi nhiệt độ thay đổi, vật liệu trong thiết bị áp lực sẽ giãn nở hoặc co lại, tạo ra ứng suất nhiệt. Nếu sự chênh lệch nhiệt độ giữa các vùng trong thiết bị quá lớn (thermal gradient), ứng suất phát sinh có thể vượt quá giới hạn chịu đựng của vật liệu, dẫn đến nứt gãy nhiệt (thermal cracking). Hiện tượng này đặc biệt nguy hiểm tại các mối hàn hoặc khu vực có ứng suất tập trung.
Theo tiêu chuẩn API 579-1/ASME FFS-1, các thiết bị làm việc ở nhiệt độ trên 400°C cần được kiểm tra nghiêm ngặt về khả năng chịu ứng suất nhiệt để ngăn ngừa hỏng hóc và đảm bảo an toàn vận hành.
Ví dụ:
- Lò hơi, thiết bị trao đổi nhiệt có thể bị cong vênh hoặc nứt do giãn nở không đồng đều.
- Thiết bị chịu nhiệt độ thấp (dưới -50°C) có nguy cơ bị giòn lạnh, mất khả năng chịu lực.
Giải pháp thiết kế:
- Sử dụng vật liệu chịu nhiệt cao như thép hợp kim chứa Cr-Mo (ASTM A387, A335).
- Tính toán hệ số giãn nở nhiệt để thiết kế kết cấu chịu nhiệt tốt hơn.
- Sử dụng các bù giãn nở (Expansion Joints) để giảm ứng suất nhiệt.
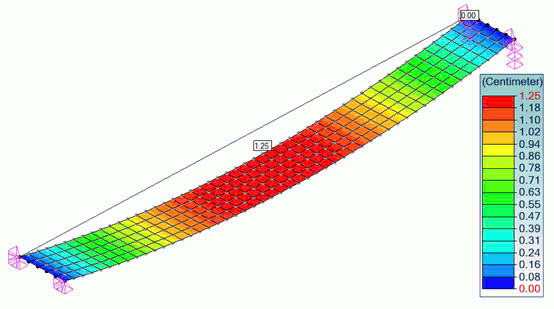
5. Tải trọng động và dao động cơ học trong thiết bị áp lực
Trong quá trình vận hành, thiết bị áp lực không chỉ chịu tải trọng tĩnh mà còn phải đối mặt với tải trọng động và dao động cơ học, có thể gây ra các hư hỏng nghiêm trọng như mỏi vật liệu (fatigue failure), cộng hưởng nguy hiểm (resonance), và hỏng hóc kết cấu.
5.1. Nguyên nhân gây ra tải trọng động và dao động cơ học
- Sự thay đổi áp suất đột ngột: Xảy ra khi đóng/mở van nhanh, kích hoạt bơm hoặc do sóng áp suất lan truyền trong hệ thống (water hammer).
- Rung động từ thiết bị quay: Máy nén, bơm, tuabin có thể tạo ra dao động cưỡng bức lên đường ống và thân thiết bị.
- Tác động từ dòng chảy: Hiện tượng xoáy dòng (flow-induced vibration – FIV) hoặc dao động do xung áp suất có thể gây hư hỏng kết cấu.
- Tải trọng do va đập: Do sự giãn nở nhiệt không đồng đều hoặc tác động cơ học từ môi trường bên ngoài.
5.2. Hậu quả và các tiêu chuẩn kiểm soát
Nếu không được thiết kế và kiểm soát đúng, tải trọng động có thể làm giảm tuổi thọ thiết bị, gây nứt mỏi hoặc phá hủy cục bộ. Các tiêu chuẩn như ASME BPVC Section VIII, API 579-1/ASME FFS-1, và EN 13445 đưa ra các phương pháp đánh giá tải trọng động, bao gồm:
- Phân tích dao động tự nhiên để tránh cộng hưởng với tần số kích thích.
- Tính toán ứng suất mỏi (Fatigue Analysis) để đảm bảo tuổi thọ thiết bị.
- Mô phỏng động lực học chất lỏng (CFD) và phân tích phần tử hữu hạn (FEA) để dự báo tác động của dòng chảy và áp suất dao động.
5.3. Giải pháp thiết kế giảm tải trọng động
- Tăng cường kết cấu: Sử dụng vòng gia cường, giảm chiều dài tự do của bề mặt chịu tải.
- Giảm biên độ dao động: Dùng giảm chấn (dampers), lò xo hoặc các giải pháp cách ly rung động.
- Kiểm soát vận hành: Điều chỉnh tốc độ đóng/mở van, lắp bộ giảm chấn áp suất để hạn chế shock áp suất.
Việc kiểm soát tải trọng động không chỉ giúp thiết bị áp lực hoạt động bền bỉ mà còn đảm bảo an toàn vận hành trong suốt vòng đời thiết bị.
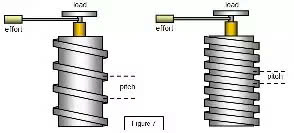
6. Ảnh hưởng của ăn mòn và tải trọng hóa học trong thiết bị áp lực
Thiết bị áp lực thường phải làm việc trong môi trường chứa các hóa chất ăn mòn hoặc chịu tác động từ phản ứng hóa học, dẫn đến suy giảm độ bền vật liệu, giảm tuổi thọ thiết bị và nguy cơ hỏng hóc nghiêm trọng. Nếu không có giải pháp thiết kế và kiểm soát phù hợp, các dạng ăn mòn và tải trọng hóa học có thể gây ra phá hủy nhanh chóng, thậm chí dẫn đến nứt vỡ giòn, rò rỉ hoặc nổ thiết bị.
6.1. Các dạng ăn mòn trong thiết bị áp lực
Ăn mòn đồng đều (Uniform Corrosion)
Đây là dạng ăn mòn phổ biến khi toàn bộ bề mặt kim loại bị tấn công bởi môi trường hóa chất. Tốc độ ăn mòn có thể được dự đoán và kiểm soát thông qua các tiêu chuẩn như API 571 hoặc NACE MR0175.
Ăn mòn cục bộ (Localized Corrosion)
Xảy ra tại một số vị trí nhất định, hình thành hố ăn mòn hoặc ăn mòn kẽ hở. Những vùng này thường xuất hiện tại các mối nối, mép hàn hoặc khu vực tiếp xúc giữa hai vật liệu khác nhau.
Ăn mòn điện hóa (Galvanic Corrosion)
Xảy ra khi hai kim loại có điện thế khác nhau tiếp xúc với nhau trong môi trường dẫn điện, tạo thành pin điện hóa. Khi đó, một trong hai vật liệu sẽ bị ăn mòn nhanh hơn so với khi hoạt động độc lập.
Nứt do ăn mòn ứng suất (Stress Corrosion Cracking – SCC)
Khi vật liệu chịu ứng suất kéo trong môi trường ăn mòn, các vết nứt có thể phát triển mà không có dấu hiệu cảnh báo. Các hợp kim thép không gỉ làm việc trong môi trường chứa ion clorua là đối tượng dễ bị SCC.
Ăn mòn do dòng chảy (Flow-Accelerated Corrosion – FAC)
Xảy ra khi vận tốc dòng chất lỏng làm mất đi lớp bảo vệ bề mặt kim loại, từ đó tăng tốc quá trình ăn mòn. Đây là hiện tượng phổ biến trong đường ống, bộ trao đổi nhiệt và các thiết bị có dòng chảy tốc độ cao.
Ngoài các cơ chế ăn mòn, một số hóa chất có thể làm thay đổi cơ lý tính của vật liệu, làm giảm khả năng chịu tải của thiết bị áp lực:
- Hiện tượng giòn hydro (Hydrogen Embrittlement): Khi hydro khuếch tán vào kim loại, vật liệu có thể trở nên giòn và dễ nứt gãy. Điều này đặc biệt nguy hiểm đối với các thiết bị làm việc trong môi trường chứa khí hydro hoặc có phản ứng điện hóa.
- Oxy hóa ở nhiệt độ cao: Các thiết bị làm việc trong môi trường oxy hóa mạnh ở nhiệt độ cao có thể hình thành lớp oxit bề mặt, làm suy yếu độ bền cơ học và tăng nguy cơ bong tróc kim loại.
- Phản ứng giữa môi chất và vật liệu: Một số môi chất có thể phản ứng với kim loại, tạo ra các hợp chất làm giảm độ bền hoặc làm giòn vật liệu, điển hình như H₂S gây nứt do hydro (Hydrogen-Induced Cracking – HIC) hoặc NH₃ gây ăn mòn kiềm (Alkaline Stress Corrosion Cracking).
6.2. Giải pháp thiết kế giảm ảnh hưởng của ăn mòn và tải trọng hóa học
- Chọn vật liệu phù hợp: Sử dụng thép không gỉ, hợp kim niken hoặc các vật liệu có khả năng chống ăn mòn cao để nâng cao tuổi thọ thiết bị.
- Bảo vệ bề mặt: Sơn phủ epoxy, sử dụng lớp lót chịu hóa chất hoặc lớp phủ kim loại chống ăn mòn để hạn chế sự tác động của môi chất.
- Kiểm soát môi trường làm việc: Loại bỏ tạp chất gây ăn mòn, kiểm soát độ pH, nồng độ oxy hòa tan và các thành phần có thể gây tác động tiêu cực đến vật liệu.
- Thiết kế giảm thiểu tập trung ứng suất: Hạn chế các khe hở nhỏ, cải thiện thiết kế mối hàn để giảm nguy cơ ăn mòn cục bộ.
- Kiểm tra định kỳ: Sử dụng các phương pháp kiểm tra không phá hủy như siêu âm (UT), từ tính (MPI) hoặc dòng điện xoáy (Eddy Current Testing) để phát hiện sớm các dấu hiệu ăn mòn và nứt gãy.
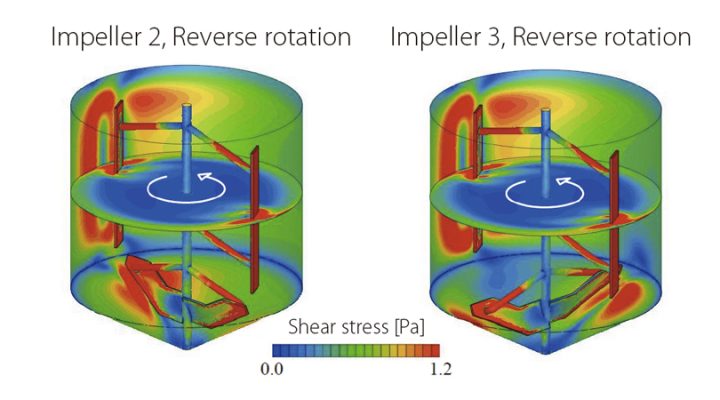
7. Tải trọng môi trường và ảnh hưởng đến thiết bị
Thiết bị áp lực không chỉ chịu tác động từ tải trọng vận hành mà còn phải đối mặt với các yếu tố môi trường bên ngoài như nhiệt độ, độ ẩm, gió, động đất và bức xạ mặt trời. Những yếu tố này có thể làm suy giảm độ bền của vật liệu, gây ra ứng suất bổ sung và ảnh hưởng đến tuổi thọ thiết bị. Nếu không có biện pháp thiết kế và bảo vệ phù hợp, các tác động môi trường có thể làm tăng nguy cơ hư hỏng hoặc mất an toàn trong quá trình vận hành.
7.1. Nhiệt độ môi trường
Thiết bị áp lực làm việc trong môi trường có biên độ nhiệt lớn có thể chịu ảnh hưởng từ sự giãn nở và co lại của vật liệu theo chu kỳ, gây ra ứng suất nhiệt lặp lại (Thermal Fatigue). Đặc biệt, trong môi trường nhiệt độ cực thấp (dưới -50°C), vật liệu có thể trở nên giòn và dễ nứt do hiện tượng giòn lạnh (Brittle Fracture). Các tiêu chuẩn như ASME BPVC Section VIII quy định rõ về giới hạn nhiệt độ và yêu cầu vật liệu phù hợp để đảm bảo độ dẻo dai trong điều kiện khắc nghiệt.
7.2. Độ ẩm và sự ngưng tụ hơi nước
Môi trường có độ ẩm cao hoặc sự thay đổi nhiệt độ thường xuyên có thể gây ngưng tụ hơi nước trên bề mặt thiết bị, làm tăng nguy cơ ăn mòn. Hiện tượng này đặc biệt nghiêm trọng đối với các thiết bị đặt ngoài trời hoặc làm việc trong môi trường biển. Các giải pháp như sơn phủ chống ăn mòn, sử dụng vật liệu không gỉ và thiết kế hệ thống thoát nước tốt là cần thiết để hạn chế ảnh hưởng của độ ẩm.
7.3. Ảnh hưởng của gió và bão
Thiết bị áp lực ngoài trời, đặc biệt là các bồn chứa, tháp chưng cất hoặc thiết bị có kết cấu cao, phải chịu tải trọng gió lớn. Gió mạnh có thể gây rung lắc, tạo ra ứng suất mỏi và làm mất ổn định kết cấu. Tiêu chuẩn ASCE 7-22 quy định phương pháp tính toán tải trọng gió và yêu cầu thiết kế phù hợp để tăng cường độ vững chắc của thiết bị.
7.4. Động đất và rung chấn
Động đất có thể gây ra tải trọng ngang đáng kể lên thiết bị áp lực, đặc biệt là các bồn chứa lớn hoặc hệ thống đường ống. Các thiết bị không được thiết kế để chịu tải động đất có thể bị lật đổ, nứt gãy hoặc rò rỉ chất lỏng nguy hiểm. Tiêu chuẩn ASME BPVC Section VIII và API 650 đưa ra các phương pháp tính toán tải trọng địa chấn và yêu cầu gia cố kết cấu để đảm bảo an toàn.
7.5. Bức xạ mặt trời và lão hóa vật liệu
Các thiết bị đặt ngoài trời tiếp xúc lâu dài với bức xạ mặt trời có thể bị suy giảm cơ tính do lão hóa nhiệt. Đối với các vật liệu phi kim loại như lớp lót polymer hoặc gioăng đệm, tác động của tia UV có thể làm giảm độ bền và khả năng chịu tải. Tiêu chuẩn ASTM G154 đề cập đến các phương pháp kiểm tra khả năng chịu lão hóa của vật liệu dưới tác động của UV.
7.6. Giải pháp thiết kế để giảm ảnh hưởng của tải trọng môi trường
- Lựa chọn vật liệu chịu nhiệt và chịu lạnh: Sử dụng thép hợp kim có khả năng chống giòn lạnh (như ASTM A333 cho nhiệt độ thấp) và thép chịu nhiệt (như ASTM A387 cho nhiệt độ cao) để đảm bảo thiết bị hoạt động ổn định.
- Thiết kế chống ăn mòn và bảo vệ bề mặt: Áp dụng lớp sơn chống ăn mòn, hệ thống cách nhiệt hoặc lớp phủ đặc biệt để hạn chế tác động của độ ẩm và muối biển.
- Gia cố kết cấu chịu tải trọng gió và động đất: Sử dụng các hệ thống neo giữ (Anchoring System), vòng gia cường hoặc bổ sung kết cấu chịu lực theo tiêu chuẩn ASCE 7-22 và API 650.
- Tăng cường kiểm tra và bảo trì: Thực hiện các phương pháp kiểm tra không phá hủy (NDT) như kiểm tra siêu âm (UT) hoặc kiểm tra từ tính (MPI) để phát hiện sớm các dấu hiệu hư hỏng do môi trường.
- Bố trí thiết bị hợp lý: Định hướng thiết bị theo hướng ít chịu ảnh hưởng của gió và bức xạ mặt trời, đồng thời có biện pháp che chắn thích hợp.