Understanding the structure and role of a steam drum not only helps ensure the safe and efficient operation of boiler systems but also minimizes risks associated with equipment failure. Any errors in the installation, operation, or maintenance of a steam drum can result in reduced performance, increased energy consumption, or even pose safety hazards to operators.
The steam drum is more than just a component of the boiler system—it is the heart of the steam generation process. Mastering knowledge of this equipment is the first step toward optimizing production efficiency and ensuring industrial safety.
1. What is a Steam Drum?
A steam drum is a crucial part of industrial boiler systems. It is a specially designed vessel that holds water and steam during boiler operation, ensuring efficient separation between these two phases. Positioned at the highest point of the boiler system, the steam drum acts as a “reservoir” for water and steam before the steam is delivered to end-use applications.
The steam drum performs three primary functions in the boiler system:
Providing Clean and Dry Steam
The primary task of the steam drum is to ensure that the steam supplied to end-use equipment, such as steam turbines, superheaters, or heating systems, is dry and free of impurities. This ensures:
- Prevention of steam carryover, which can damage equipment.
- Avoidance of issues such as water hammer and corrosion caused by wet steam.
- Optimal performance of steam-utilizing equipment.
Maintaining a Reserve of Saturated Water
The steam drum serves as a small reservoir of saturated water within the system. This function supports:
- Quick responses to fluctuations in steam demand without disrupting system operation.
- Stabilization of boiler pressure and temperature, ensuring overall system reliability.
Managing Internal Water Treatment
Water treatment processes are also conducted within the steam drum, including:
- Mixing internal treatment chemicals to control water properties, such as total suspended solids (TSS) and total dissolved solids (TDS).
- Conducting blowdown procedures to remove impurities, thereby maintaining water quality and extending the system’s lifespan.
2. Structure of the Steam Drum and its Operating Principles
2.1. Components of the Steam Drum
2.1.1. Feedwater Inlet
The feedwater inlet is where water is introduced into the steam drum, playing a crucial role in maintaining a stable water supply for the entire boiler system. Its design includes flow distribution structures that minimize turbulence as water enters the drum. This ensures even water dispersion within the drum, optimizing the steam-water separation process.
Moreover, the feedwater inlet is typically made from high-pressure-resistant materials that can withstand the thermal and chemical conditions of the system. The connection to the steam drum is sealed to prevent leaks, ensuring safe and efficient operation.
An important consideration is controlling the feedwater temperature. If not properly regulated, significant temperature differences between the water and steam can create thermal stress, reducing the lifespan of the steam drum.
2.1.2. Steam Outlet
The steam outlet is the point where dry steam is collected and delivered to end-use equipment, such as steam turbines or heat exchangers. The outlet’s design is critical to ensure that steam leaving the drum is free from water droplets or impurities.
At this stage, steam separators are often installed to remove water completely. These separators work by slowing the flow, allowing water droplets to settle while steam continues upward. This process produces high-quality dry steam, preventing carryover that could severely damage downstream equipment.
The steam outlet is typically constructed from heat- and pressure-resistant steel, designed to maintain durability under harsh operating conditions.
2.1.3. Baffle Plates
Baffle plates are internal partitions within the steam drum, strategically positioned to direct the flow of water and steam while enhancing phase separation. As water and steam move through the baffle plates, the flow rate decreases, allowing water droplets to settle at the drum’s bottom while steam rises to the top.
These plates are typically made from corrosion-resistant metal and are designed to ensure efficient phase separation without obstructing flow. Additionally, they help prevent internal vibrations in the steam drum, ensuring system stability.
2.1.4. Safety Valves
Safety valves are essential protective devices in the steam drum, designed to automatically release pressure when it exceeds safe levels. These valves provide instantaneous pressure relief, preventing potential explosions that could cause significant system damage.
Safety valves are usually positioned at the top of the steam drum, where pressure is highest. They are manufactured from high-quality materials capable of withstanding extreme temperature and pressure, ensuring long-lasting performance and reliability.
The safety valve operates automatically through a spring mechanism calibrated to a specific pressure. When the pressure exceeds the threshold, the spring expands, opening the valve to release pressure. Once the pressure returns to a safe level, the valve closes, maintaining system stability.
2.1.5. Blowdown Line
The blowdown line, located at the bottom of the steam drum, is responsible for removing excess water, sediment, and impurities that accumulate during operation. Regular blowdown procedures help maintain water quality and prevent scale buildup, a primary cause of corrosion and decreased boiler efficiency.
The blowdown process is conducted periodically, with control valves ensuring that it does not disrupt system operations. The blowdown line is typically made from pressure-resistant steel with an anti-corrosion coating to withstand the harsh conditions inside the boiler environment.
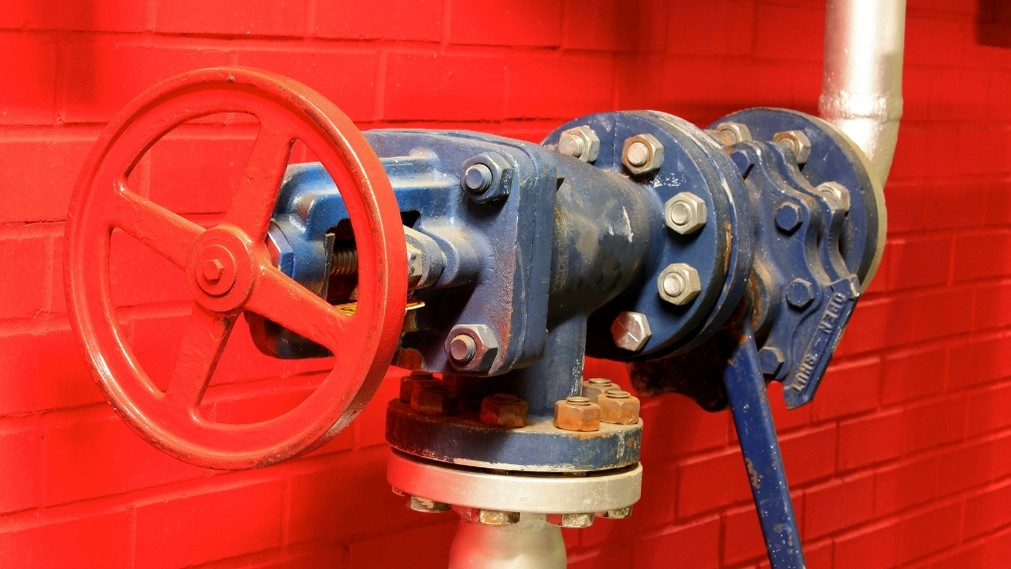
2.1.6. Sensors and Gauges
Sensors and gauges are indispensable auxiliary devices that provide real-time data on pressure, temperature, and water level within the steam drum. These devices enable continuous monitoring and system adjustments to maintain all parameters within allowable limits.
The pressure gauges are installed in easily visible positions, allowing operators to monitor the drum’s status accurately. These devices not only facilitate efficient operation but also help detect potential issues early, reducing risks and optimizing overall system performance.
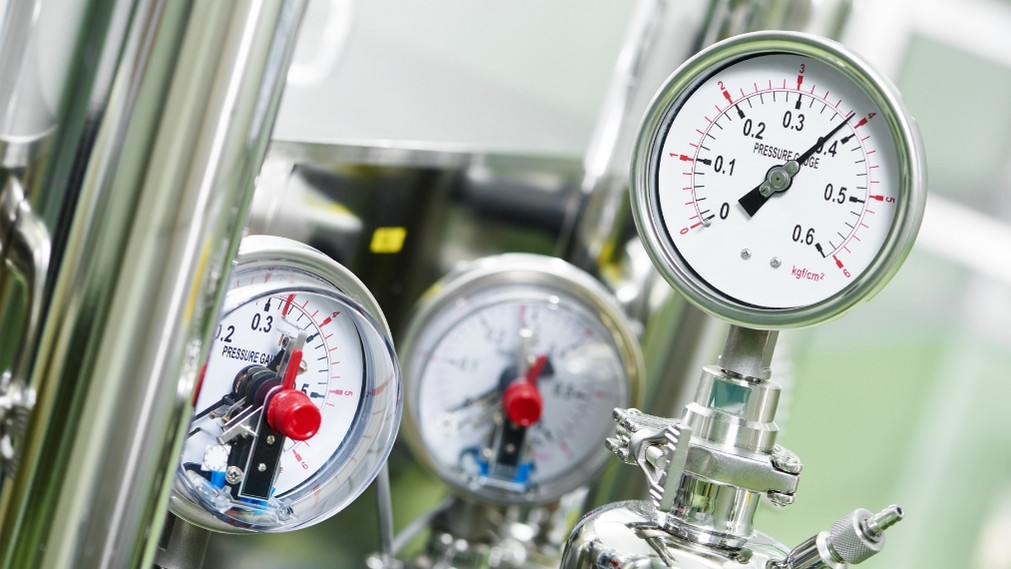
>>>Learn more about Prebecc’s fabrication and installation services
2.2. Operating Principles of the Steam Drum
The operating principles of the steam drum are based on phase separation, utilizing the density difference between water and steam, as well as the synchronized operation of its components.
2.2.1. Phase Separation and Dry Steam Supply
When feedwater enters the steam drum through the feedwater inlet, it is evenly distributed via flow-guiding structures. The water, heated by the boiler, evaporates to form a mixture of water and steam, which moves upward. At this point, the baffle plates slow the flow, allowing larger water droplets to settle while the steam continues to rise.
Before the steam exits the drum through the steam outlet, it passes through steam separators. These devices employ centrifugal or physical barriers to remove any remaining water particles, ensuring the steam achieves high dryness. This not only enhances system efficiency but also protects downstream equipment, such as turbines or heaters, from corrosion and damage caused by water.
2.2.2. Water Quality Regulation and Control
Within the steam drum, water is maintained in a saturated state to ensure system stability. Impurities such as sludge, minerals, or unwanted substances accumulate at the bottom of the drum and are expelled through the blowdown line. This process not only improves water quality but also prevents scale buildup on heat exchange surfaces, which can reduce efficiency and increase the risk of corrosion.
The integrated sensors and gauges continuously monitor critical parameters such as pressure, temperature, and water level. If any values exceed the threshold, the safety valves are triggered to release excess pressure, safeguarding the entire system.
2.2.3. Coordination of Components
The operation of the steam drum relies on the seamless coordination of its components. The feedwater inlet ensures a steady water supply, the baffle plates and steam separators optimize phase separation, and the safety valves and blowdown line maintain stable operation. Thanks to this integrated design, the steam drum can deliver clean, dry steam that meets stringent technical requirements during production.
3. Materials and Technical Standards of Steam Drums
The steam drum is a critical component of boiler systems, operating under high pressure and extreme temperatures. Therefore, the choice of materials and compliance with technical standards are decisive factors for system performance, durability, and safety.
3.1. Materials for Manufacturing Steam Drums
Steam drums are typically constructed from high-quality alloy steels designed to withstand harsh pressure and temperature conditions. Commonly used materials include:
- Carbon Steel: Materials like ASTM A106 or ASTM A515 are commonly employed in medium-temperature environments. Carbon steel offers high-pressure resistance and cost-effectiveness.
- Low Alloy Steel: In higher temperature and pressure settings, low alloy steels such as ASTM A335 (P11, P22) are preferred due to their excellent mechanical strength and oxidation resistance. These steels contain elements like Chromium (Cr) and Molybdenum (Mo) to enhance heat resistance and corrosion resistance.
- Stainless Steel: For systems requiring superior corrosion resistance, stainless steel grades like ASTM A240 (304, 316) are utilized. These materials are suitable for environments with chemicals or weak acidic condensates.
- Heat-Resistant Steel: For boilers operating at extremely high temperatures, materials like Inconel or high Chromium-Nickel alloy steels are selected. These materials maintain structural integrity at temperatures exceeding 600°C.
3.2. Technical Standards for Steam Drums
Steam drums must be designed and manufactured in compliance with international standards to ensure safety and efficiency. Commonly applied standards include:
ASME Boiler and Pressure Vessel Code (BPVC):
- ASME BPVC Section I: Standards for boilers and steam drums used in high-pressure environments.
- ASME BPVC Section VIII: Standards for the design and fabrication of pressure vessels, including steam drums in specialized systems.
EN 12952/12953: European standards for the design and fabrication of water-tube and fire-tube boilers, covering steam drums. These standards outline requirements for materials, welding, and quality inspection.
API 530: Applicable to the design of heat exchangers in the oil and gas industry and extendable to steam drums under high-temperature conditions.
ISO 16528: An international standard for pressure equipment, guiding material selection and safety inspections for steam drums.
3.3. Material Testing and Certification
Every batch of material used for manufacturing steam drums undergoes stringent testing procedures, including:
- Mechanical Testing: Evaluating tensile strength and yield strength.
- Impact Testing: Conducting Charpy impact tests for toughness.
- Chemical Composition Analysis: Ensuring the material meets specified technical requirements.
Additionally, materials must be certified by reputable organizations such as ASTM, EN, or ISO to guarantee quality and operational reliability under extreme conditions.
Tham khảo: https://savree.com/en/encyclopedia/boiler-steam-drum